Al Anwar invests in dry grinding technology
April saw the completion of the fifth line installed in the Nizwa production plant of Al Anwar Ceramic Tiles Co., Oman's largest producer of ceramic floor and wall tiles. The new line has a daily capacity of 14,000 sq.m of double-fired floor and wall tiles, taking the production capacity close to 20 million sq.m/year.
In order to reduce energy costs and enhance competitiveness, together with this latest investment, the ceramic tile company renovated the preparation plant in its third line, by substituting a wet preparation line with the MS-Drytech dry grinding technology supplied by Manfredini & Schianchi (the same technology was already installed in 2004).
In the system supplied by Manfredini & Schianchi, the primary milling takes place on the P.I.G.HD mill, while a Molomax 6/500 mill is used for the subsequent refining phase. The Molomax can produce more than 30 tonnes per hour, with a separation cut of less than 63 microns, guaranteeing an end product with seamlessly smooth surfaces - ideal for the application of ultra-gloss enamels and digital decorations.
The agglomeration and humidification is entrusted to a Madirex granulator (protected by a global patent), a system that is currently seen as a technological landmark in the granulation of dry-milled powder. The technical benefits of using Madirex include:
- productivity of up to 40 tonnes per hour;
- electricity consumption of
- no heat consumption;
- negligible maintenance costs;
- small space needed for installation, and the system can be easily adapted to existing machines;
- a constant particle size distribution curve with an extremely high percentage of granular material, ideal for pressing large format tiles.
Certified to ISO 9001 standard since 2006, the Al Shams range made with the MS-Drytech dry technology includes wall tiles in the formats 25x33 and 25x40 cm, and floor tiles in the formats 33x33, 45x45 and 50x50 cm.
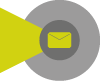
Did you find this article useful?
Join the CWW community to receive the most important news from the global ceramic industry every two weeks