Ceramica Almeida adopts dry grinding technology for porcelain tile production
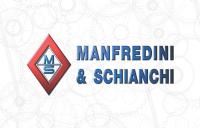
Ceramica Almeida, a leading Brazilian ceramic tile manufacturing group based in the Santa Gertrudes (SP) district since 1938, started up a new facility in early September for the production of porcelain tile using dry grinding technology supplied by Manfredini & Schianchi.
The innovative raw materials preparation line has a production capacity of 25 ton/h and feeds a Siti B&T plant designed for an output of around 550,000 sq.m/year of porcelain tiles in 60x60 cm and 60x90 cm sizes with a cycle time of around 40 minutes. These outstanding technological results stem from an analysis of various local raw materials and the combined work over the last three years of the Manfredini & Schianchi Technology Centre, Brazilian ceramic research centres and the team of expert engineers from Ceramica Almeida. The finished product has the same characteristics of water absorption, mechanical strength and aesthetic quality as porcelain tile produced using wet grinding technology.
To build the plant, Manfredini & Schianchi introduced the concept of “open cycle” grinding complete with airflow drying (suitable for incoming raw materials with a moisture content of up to 17%). This allows for the production of a perfectly uniform ceramic mix with constant moisture content and a very fine particle size (45 microns).
The hot air entering the mill is recovered from the kiln cooling process, thereby minimising energy consumption.
The new-generation finishing pendular mills (Molomax 6/190 Mega) guarantee high levels of performance even for fine milling and with raw materials of various types and hardness. The ceramic mass is mixed uniformly inside the grinding chamber to achieve the optimal degree of homogenisation for the subsequent granulation stage, where the Madirex system produces a spherical granule without the need for a drying process. The fully-automated Madirex system is perfectly consistent with the new Industry 4.0 technology. It is equipped with control software and is capable of independently managing the entire granulation process, adjusting automatically for unexpected variations in moisture content.
Next year Ceramica Almeida is planning a further plant upgrade when the granulation system will be completed with installation of the Fusion F.G.T. technology tower (patented worldwide), which is capable of producing a porcelain agglomerate with a flowability index and mould filling capacity similar to the best spray-dried powders.
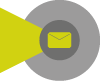
Did you find this article useful?
Join the CWW community to receive the most important news from the global ceramic industry every two weeks