Cerdomus starts up a new slab production plant
Cerdomus started up in the summer its new line in Castel Bolognese (Ravenna), equipped with Sacmi’s leading technologies, including the Continua+ PCR 2000.
An icon of Italian ceramic creativity for more than 50 years renowned in particular for its original sizes, surfaces, material effects and processing, Cerdomus has now stepped decisively into the large slab production arena with this summer’s start-up of a new complete plant at its site in Castel Bolognese (Ravenna), which will be able to produce upward of 8,000 sqm/day of decorated slabs of various sizes and thicknesses.
After collaborating for many years with Sacmi on traditional size products (up to 600x1200 mm), for this new project initially launched in 2021 Cerdomus chose Continua+ technology as the centrepiece of a production line that also includes the Imola-based group’s other leading technologies, such as the dryer, kiln, digital printers and finishing lines.
A market leader with its “Creative ceramic collections”, Cerdomus has combined an innate passion for design with a constant focus on technological innovation in order to consistently deliver the highest level of quality with all the style and character of Italian ceramics.
“Our brand has a clear market identity,” notes Cerdomus Chairman Paolo Turbati. “Ceramics is one of the oldest materials in the world and we have always seen it as a source of inspiration for creating unique installations, building on our strengths to deliver the widest range of combinations, sizes, thicknesses, decorations, styles and material effects. We chose Continua+ for this latest project as it is the world’s leading technology in this sector.”
Specifically, Cerdomus opted for a new PCR 2000, the globally best-selling member of the Continua+ family.
“Along with large slabs, we’re also interested in the possibility of achieving coordinated, flexible and efficient production of all the sub-sizes and furnishing accessories that are highly popular with our customers today,” continues Turbati. “This solution fits in perfectly with the Cerdomus philosophy of coordinated collections, high quality and product aesthetics.”
The new line will enable Cerdomus to produce sizes up to 1600x3200 mm, essentially meeting all market demand for both larger sizes and coordinated sub-sizes.
In the adopted configuration, spray-dried powder from the existing body preparation plant (also supplied by Sacmi) feeds both the conventional presses and the new Continua+.
“This versatility was another important factor,” continues Turbati. “Being able to work with the same bodies as the traditional presses made it possible to accelerate the start-up stage and begin producing the new sizes immediately.”
The complete plant
After leaving the Continua+, the slabs are fed into the new Sacmi ECP 295 dryer equipped with an automatic loading and unloading system. From there they are fed into an FMA Maestro kiln optimised for this type of product, thereby guaranteeing consistently superior quality and reducing potential defects. The plant is also equipped with all the latest-generation solutions for reducing consumption and emissions.
After leaving the kiln, the slabs proceed to the squaring, splitting and polishing lines built by BMR, the Sacmi Group company specialising in ceramic product finishing with distinctive solutions for automation, Industry 4.0 flow management, reliability and efficiency. Here too, Sacmi supplied the loading and unloading equipment.
To further expand the scope for enhancing product aesthetics, Cerdomus chose to combine the existing decoration lines with a new DHD 1812 digital decorating machine. This solution can accommodate up to 12 colour bars, 8 of which are already operational, for the coordinated application of inks and material effects.
Sacmi will also supply laser-guided handling equipment for the complete automation of factory logistics.
“The Cerdomus project rewards our approach to ceramic system design,” comments Sacmi Chairman Paolo Mongardi. “While technologies like Continua+ are ideal for producing new high-quality products, in general our customers have always appreciated our plant engineering philosophy and our ability to act as a one-stop shop, supplying state-of-the-art technology for every stage of the production process.”
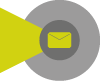
Did you find this article useful?
Join the CWW community to receive the most important news from the global ceramic industry every two weeks