EGE Seramik goes for the Sacmi-built EKO kiln
A long-standing partner of the Sacmi Group, EGE Seramik has once again commissioned the Imola-based cooperative to modernise its plant number 4 and upgrade its body preparation department.
Sacmi has supplied two PH6500 presses, the perfect choice for manufacturing 600x600 porcelain tiles. These feature 3-cavity moulds and fast production cycles and have been supplied complete with moulds, accessories and the relative vertical driers; Sacmi has also supplied complete glazing lines plus storage solutions for fired/unfired items featuring magneto-guided vehicles.
The most important part of this order was - for the very first time in Turkey - the latest-generation 145-metre-long EKO kiln with a 2950 mm wide inlet. This takes the place of the 2 old dual-channel kilns installed back in the early 80s. In addition to containing costs (at record lows for the Turkish porcelain tile industry, thanks to the EKO’s integrated heat recovery system), it also offers outstanding performance in terms of colour tone and tile dimension, advantages greatly appreciated by Ege Seramik’s technicians.
This plant upgrade also included a complete new sorting line by Nuova Fima, the Sacmi Group brand specialising in end-of-line solutions; this features all-new EKOWRAP technology, an innovative solution capable of cutting cardboard use by up to 65%, thus increasing output rates and boosting production to over 10,000 square metres a day.
Modernisation of the grinding department saw the replacement of a large number of discontinuous drum mills with a new MMC 180 modular mill which, combined with an ATM200 spray drier, makes the body preparation department one of the highest-performing in Turkey. Compared to the earlier drum mills, the new modular mill provides energy savings of around 40% and, above all, reduces labour, maintenance and running costs.
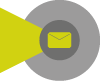
Did you find this article useful?
Join the CWW community to receive the most important news from the global ceramic industry every two weeks