Hayal installs Sacmi’s largest and most powerful mills and spray dryers
In order to significantly boost productivity, the Turkish group Hayal has purchased the largest and most powerful ceramic mills and spray dryers ever launched onto the market, supplied by Sacmi.
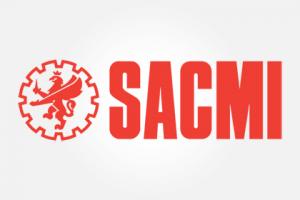
Size matters. As part of its plans to significantly boost productivity in 2023, the Turkish group Hayal has chosen to increase the size of the machines in its body preparation department by purchasing the largest and most powerful ceramic mills and spray dryers ever launched onto the market.
A construction materials producer specialising in ceramic tiles, the Hayal Group already took a big step forward in 2016 when it installed its first Sacmi mills and spray dryers. The company is now looking to the future and has commissioned Sacmi to supply the new MMC240 and ATE350 units, the largest machines of their kind ever built, for the Qua Granite production facility in Söke (Kuşadasi district).
So why choose such large machines? The main reason is to increase productivity in response to the anticipated growth in market demand, for which purpose Hayal is planning to reach a total capacity of 50 million sqm by 2023. Another key aim is to achieve a high level of product standardisation, thereby optimising economic and organisational aspects of the production process. In response to the growing trend towards ever larger body preparation machines that has been underway for the last 15 years, Sacmi has focused on developing these kinds of solutions and as a result has now installed a record of almost 1,000 MMC continuous modules and 1,600 ATM, ATE and ATI spray dryers worldwide.
The first ATE350 spray dryer is already running at full capacity at the Söke facility and is fed by two MMC240 modular mills with an output of up to 90 tonnes per hour, while the second section of the line with a further two MMC240s and an ATE350 is scheduled for start-up in early 2023. Following the success of this first shipment, the Turkish group has already placed further orders for this type of spray dryer for installation in other production units in 2023.
In contrast to the trend of small batches and frequent changes of products and consequently raw materials popular in some markets, the Sacmi range taps into the clear global demand for increasingly high-performance body preparation machines. This approach offers a number of advantages. Firstly, for the production of ceramic products that do not require specific full-body effects, it is becoming increasingly common and cost-effective to produce large volumes of standard bodies which are subsequently machined, textured and digitally decorated.
Other factors concern the way the machines are designed in relation to the specific characteristics of the grinding and spray drying process. The MMC240 mills are the first machines on the market that Sacmi has configured with 4 modules at the customer’s request, while further solutions with up to 5 modules are being supplied in other parts of the world.
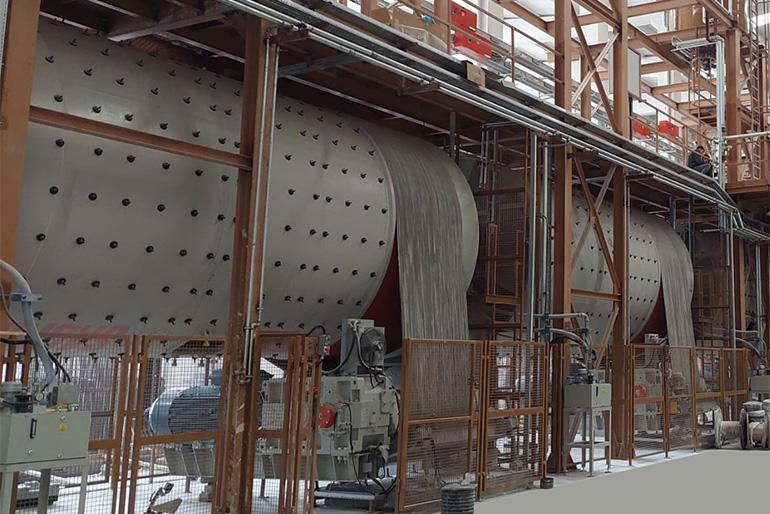
Originally developed by Sacmi in 2005, the modular mill is still the most flexible and efficient way of controlling the various grinding stages from crushing through to fine milling. The addition of a fourth or even a fifth module introduces an extra control parameter, further optimising the process according to product characteristics and thereby saving energy.
Spray dryers are a different matter. Along with the characteristics of cost-effective design, operation and maintenance typical of the entire Sacmi ATE range, the higher-volume models also deliver a more than proportional increase in efficiency. The installation of a single ATE350 can bring an increase in efficiency of up to 1.5% compared to the use of two ATE180s (with the same output), effectively saving 250,000 standard cubic metres of gas per year. This means a faster return on the investment, up to a 20% smaller footprint for the same output and a simpler plant design (fewer batching stations, conveyor belts, etc.). These machines are designed and sized to operate 24/7 with the quality, control and reliability for which Sacmi is renowned.
But Hayal’s investments in Sacmi technology don’t end here. In addition to the projects already scheduled for 2023, the Söke plant will soon be supplied with ten new PH 5200 presses, the market benchmark for pressing medium to large sizes such as 600x600 mm and 600x1200 mm.
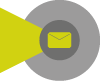
Did you find this article useful?
Join the CWW community to receive the most important news from the global ceramic industry every two weeks