Lingl: new partnerships in Russia
Last July, an important business partnership was concluded between Lingl and OOO Kemma, a brick manufacturer based in Chelyabinsk, Russia. The brickworks will be equipped with new machinery for wet side products, dryer car loading and unloading, storage of drying support material and a new setting line. The objective is to increase output from the current 80 million to 120 million units per year. The new performance parameters also require a retrofitting of the existing kiln with the respective equipment. In the picture: Andreas Lingl, Managing Director of Lingl and Ivan Gornov, Chief Executive of Kemma (on the left).
Again in Russia, Lingl had successfully tested in May the production facility supplied to OAO Pobeda LSR, a hollow brick manufacturer, which is part of the LSR Group based in Saint Petersburg. The high flexibility of the new plant allows for the production of six brick types, from standard size 2.1 to standard size 14.3, realised in compliance with the latest product quality European standards, and with particular attention paid to energy-efficient technology solutions (after the tests, the values of energy consumption were even below the agreed guaranteed values).
Pobeda LSR, established in 2005 by the fusion of three brickworks (Pobeda, Keramika and Lenstroykeramika), was the first company in the country to produce hollow bricks of large size and to launch them on the market under its own brand, "Rauf". Lingl supply includes all machines and plant components, the control system for wet and dry side, setting installation, unloading and packing. A Universal cutter is used for cutting large-size bricks, whereas the small sizes are produced by means of a belt harp. The loading of dryer cars is carried out by a loading rake. The drying time of the continuous compact dryer, equipped with rotary fans, is 24 hours. The tunnel kiln has been designed for a capacity of 700 t / day which corresponds to a plant capacity of 120 million strand size pieces per year. Two setting robots are used for loading the kiln cars, ensuring a flexible and accurate operation. Another robot installation carries out the unloading and packing operations. Special software, as well as a tracking system for tunnel kiln cars and a management information system are used to collect all the process, energy consumption and maintenance data. These systems also acquire and evaluate the data related to the preparation and shaping phases.
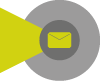
Did you find this article useful?
Join the CWW community to receive the most important news from the global ceramic industry every two weeks