Power, automation and 4.0 control: the complete Sacmi Tiles range at Tecnargilla 2018
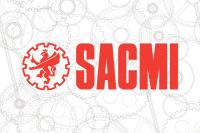
More powerful, more flexible continuous compaction, higher-performing integrated-automation traditional presses, line supervisors that interface directly with the customer's ERP, new plant and warehouse flow management solutions, fully digital glazing and decoration line control. These are the keystones of the Sacmi range that will be showcased at the international Tecnargilla fair in Rimini.
Visitors can enjoy a sneak peek of the new PH16000, the latest new-generation, integrated-automation press that can handle tiles as large as 1200x2400 mm (i.e. large slabs). This latest machine (a powered, working example of which will be exhibited at Sacmi Imola throughout the fair, with guided tours and special events for customers) offers several advantages. Above all, the press belongs to the new Smart Series which, thanks to more powerful, integrated communication based on the Ethernet Powerlink field bus, ensures accurate control of all machine parameters, including consumption. Then there is its usability, which stems from a user-friendly interface that provides valuable diagnostic information and cutting-edge design features such as the latest version of proportional electronic lifting.
Another key feature of the Sacmi PH16000 is the automatic mould changeover system: developed by Sacmi Imola together with Sacmi Molds&Dies, the patented CRS system, which has enjoyed worldwide success, allows moulds weighing several tons to be changed in complete safety and very quickly, thus combining power and speed with outstanding flexibility.
Moving on from press to compactor, Sacmi will also be showcasing the new PCR3000, the very heart of the latest Continua+ line which, with over 40 solutions sold globally, has set the industry standard for manufacturing large decorated slabs of varying size and thickness. Now able to produce even thicker tiles up to 1800 mm wide (compared to a previous maximum of 1600), the new high-potential module will be exhibited inside a dedicated area. In addition to the new APB3000 powder feeder, redesigned to handle the larger slabs produced by the compactor, upstream from the PCR visitors will also see the new DDD3000 dry digital decoration module (the latest Sacmi Digital gem, which complements the company's patented full-body veining system).
The final frontier of large ceramic kitchen tops, through-body veining is a must-have when the product demands a certain level of aesthetics on its edges. In addition to the already-patented veining system, Sacmi has now developed a new vein vision system (SVV); this uses complex software-graphics to put the slab through successive high-resolution digital decoration processes to multiply aesthetic yield.
Further Intesa-Sacmi Digital solutions will include several exhibited modules that pave the way for complete digitalization of the glazing and decoration line. Perfect synchronism between dry and wet decoration systems - starting with the new DDG1422 (Digital Dry Glazing for the deposit of glazes and grains) - lets manufacturers produce unmatched on-tile 'tactile' and depth effects in response to the latest trends on the global slab market.
Last but not least come drying and firing, crucial stages of the ceramic process in which the CMC and Sacmi Forni range play a pivotal role. Visitors to Rimini will have the opportunity to get a close look at the new 7-tier E7P2950 dryer and the high performance, energy saving modulated-air FMA2950 kiln. Alongside the technology, Sacmi is equally ground-breaking when it comes to design: it has, in fact, fully remodelled the layout of the machines and optimised their footprints.
Sacmi is a pioneering designer of new line supervision and warehouse control solutions and will be displaying the latest version of the H.E.R.E. (Human Expertise for Reactive Engineering) platform. The cornerstone of the new factory 4.0 concept, the H.E.R.E system has already been successfully installed by major international ceramic players. The supervisor lets manufacturers act on plant flows retroactively (i.e. by combining monitoring and predictive diagnostics with true order scheduling functions as part of a wider make to order logic); alongside this, Sacmi provides complete end-of-line integration by implementing state-of-the-art technology and redesigning semi-finished item warehousing to achieve outstanding automation that is personalised according to customers’ needs, manufacturing facilities and markets.
The latest innovation from Nuova Sima, the Sacmi Group's specialist in handling and logistics, illustrates this point perfectly. The picking island (with an innovative Gaiotto robot-controlled system that loads slabs into crates or on stands) will be set up at Tecnargilla in a dedicated area so visitors can experience for themselves the future of ceramics 4.0.
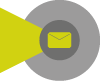
Did you find this article useful?
Join the CWW community to receive the most important news from the global ceramic industry every two weeks