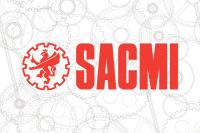
Twice as much floor space for the Sacmi Imola Sanitaryware laboratory - a pivotal international facility for firms in the industry - and an ambitious investment plan for a new machine pool that will give the lab permanently increased operating capacity. With new developments like these, the Sacmi Imola Sanitaryware & Tableware Division is clearly upping the pace as it approaches Tecnargilla 2018, the not-to-be-missed fair that will, this year, see the Group out in force to showcase cutting-edge technology and machines.
As in previous years, the Open Day organised for the first day of the fair (24 September) is particularly important for the division: here, existing and potential customers will have a great opportunity to visit the new laboratory and continue, in the afternoon, with a guided tour of another highly successful firm (this year customers will be taken to the Ducati Motors production plant).
With regard to the lab machines and equipment, the pilot plant area - where floor space has now been doubled - will display the two new ALV and AVI casting modules. Here, visitors can witness one-piece WCs of complex shapes being cast. Alongside them stands the new glazing cell with the GA-OL dry filtration system, the flagship product from Gaiotto, the leading provider of robotized glazing solutions to the Italian sanitaryware industry. Lastly, the Riedhammer shuttle kiln with high performance Reko burners is a top-of-the-range sanitaryware firing solution that combines maximum performance with low consumption.
The same Open Day will also include a visit to the modelling department, where Sacmi recently inaugurated the new CAD/CAM machining centre, plus a look at the new fired item 3D inspection unit which mounts an array of HD video cameras. The department also features the all-new unit for the manufacture - with precision numerical control systems - of large, complex WCs. This decidedly future-oriented unit goes hand-in-glove with the experience and expertise of the workers who prepare the plaster moulds from which mother-moulds and final moulds are obtained.
Combining high productivity with the ever-greater flexibility demanded by modern sanitaryware-tableware markets will be a key theme of our participation at Tecnargilla, as the exhibited robotized product handling unit will clearly demonstrate. In practice, then, the process is fully automated from dryer to kiln loading, without any need for worker intervention. More specifically, alongside two AVB casting cells working in conjunction with Fanuc handling robots, the Sacmi stand will also showcase a glazing cell with two GA2000 robots; the latter feature the ground-breaking Sacmi GDA 80 needleless spray gun, which eliminates the need for maintenance while boosting quality. The entire process is aided by latest-generation laser-guided cars that convey products from the dryer to the glazing station and then on to the kiln.
Sacmi H.E.R.E. (Human Expertise for Reactive Engineering) will also play a leading role at Tecnargilla. As with tiles, H.E.R.E. allows comprehensive tracking of sanitaryware manufacturing. Both casting cells exhibited at Rimini will be equipped with the pioneering interface, which incorporates on-machine use and maintenance manuals. In practice, the use and maintenance manual is presented to the worker contextually following a warning or alarm. To identify and order spare parts, instead, all the worker has to do is click on the component in the on-machine e-manual. Doing so provides a real-time 3D view and task information. The system itself will then generate a file with which to order, if needed, the spare part.
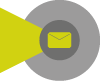
Did you find this article useful?
Join the CWW community to receive the most important news from the global ceramic industry every two weeks