The Castellón ceramic cluster grows with SITI B&T technologies
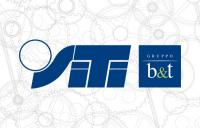
SITI B&T Group has won a large number of orders in Spain’s Castellón ceramic cluster in recent months, confirming the group’s role as a major technology partner for the top Spanish tile producers.
Baldocer, a leading company based in Vilafamés, has confirmed its complete trust in the Italian group’s technologies with the installation of two new high-productivity, high-efficiency lines for the production of large-format glazed porcelain tiles. The plant includes XL EVO 7608/2450 presses, dryers and kilns with high levels of energy efficiency and productivity. SITI B&T’s Group’s role as a system integrator is also underscored by the squaring and honing machines supplied by member company Ancora.
Alcora-based company MYR Cerámica has also made substantial investments aimed at transforming its factory, including the installation of an XL EVO 6608/2450 press complete with E-Syncro demoulding system, 5-layer dryers and storage and handling systems for medium to large size tiles. The use of Titanium® technology in the single-channel kiln has enabled MYR to reduce both energy consumption and atmospheric emissions while achieving higher levels of productivity. A high-speed dry squaring system from Ancora is integrated into the plant.
Cicogres has adopted Titanium® technology at its facility in Vilafamés with the aim of increasing production capacity and adding value to products with the introduction of new sizes and product types. Here too it has improved energy efficiency by drastically reducing production costs and emissions. Ancora technologies for squaring, honing and surface protection of materials have been installed in the end-of-line stage. A latest-generation automatic storage system guarantees the flexibility and efficiency of the plant.
Stylnul (STN Cerámica), one of Spain’s largest ceramic producers, has doubled the production capacity of its Azulmed facility with a new fast high-efficiency line comprising an EVO 5008/2450 press, a 7-layer dryer with 4000 mm entrance width for large sizes (a world first for the ceramic industry), and a Titanium® kiln with 3500 mm entrance width. A dry score-and-snap cutting machine from Ancora has been installed at the kiln exit to optimise finished product processing and guarantee a higher percentage of first-choice products.
Equipment has also been supplied to Tierra Atomizada Group (L’Alcora) and Compacglass (Onda), a member of the Pamesa Group. Tierra Atomizada has installed a 25,000-litre Siti B&T spray dryer that guarantees high levels of flexibility, productivity and energy efficiency, while Compacglass has adopted an XXL Titanium® 3500 double-channel kiln of length 160 metres (the largest in operation in Europe) complete with a hot air recovery system.
All installations were carried out with the support of B&T Iberica, the subsidiary which has enabled SITI B&T Group to deliver cutting-edge technology and guarantee an impeccable service in the Spanish market since 1981.
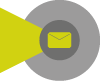
Did you find this article useful?
Join the CWW community to receive the most important news from the global ceramic industry every two weeks