Fornaci di Manzano: the new line from Marcheluzzo
The company has commissioned Marcheluzzo to supply solutions that further improve the thermal and acoustic insulation performance of its rectified blocks.
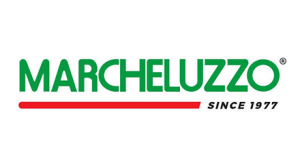
Fornaci di Manzano, a long-established Italian company operating in the Friuli region since the early 1900s, specialises in the production of masonry blocks, including both traditional solutions and versions with high thermal and acoustic performance.
Under the astute management of owner Stefano Midolini and his sons Marco, Michele and Mario, the company has continued to invest in innovation, expanding its range to include latest-generation thin-walled blocks with rectified bedding surfaces for more sustainable construction.
In line with this commitment, the company has commissioned Marcheluzzo to supply solutions that further improve the thermal and acoustic insulation performance of its materials.
Thin-walled rectified blocks: all the advantages
Rectified clay blocks represent a significant innovation and allow for the construction of high-performance masonry thanks to precision rectification technology and the presence of thin webs that create multiple air chambers, improving insulation and simplifying installation.
Rectified blocks are produced with perfectly flat and parallel bedding surfaces, allowing them to be installed with a thin layer of adhesive between each course, eliminating the thermal bridging associated with traditional mortar joints. This also reduces mortar consumption, resulting in material savings and faster and more precise installation.
The new line from Marcheluzzo
Marcheluzzo began collaborating with Fornaci di Manzano in early 2024 in response to the brick manufacturer’s request for new technology that could be flexibly integrated into its existing fired product unloading line. The new plant partially retains the existing set-up while fully automating the system for removing layers of fired products from the kiln cars. This includes transfer via a modern chain and toothed belt conveyor system to the grinding machine used to rectify the two bedding surfaces, which are sized according to the customer’s specifications.
The rectification process is an innovative solution developed in collaboration with a leading company in the ceramic sector. The system operates progressively, with the installation of a sequence of abrasive discs, each with a specially designed diamond configuration to optimise material removal based on the characteristics of the raw material used. The discs remove a minimal quantity of material from the clay blocks, reducing mechanical stress and ensuring a surface finish that allows for correct application of adhesive during installation on-site.
The entire system is controlled automatically from the kiln car unloading stage through to the forming of transport-ready packs sized according to number of pieces and pallet weight. Marcheluzzo has also installed a powerful dust extraction system which efficiently removes dust generated during dry machining through strategically placed extraction points inside a soundproofed grinding booth, ensuring a healthy and dust-free environment during fired product machining.
This project once again testifies to Marcheluzzo’s ability to provide the best possible solution to customers’ needs.
An in-depth analysis of the production process has resulted in a high hourly output while delivering innovative, high-performance products that improve the energy efficiency of buildings.
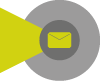
Did you find this article useful?
Join the CWW community to receive the most important news from the global ceramic industry every two weeks