Ink-Jet Defender by Cami
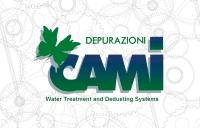
The compartments where digital decoration machines are installed are inevitably subject to the ingress of air and dust from surrounding areas. This problem is exacerbated by the presence of the extraction systems needed by many digital systems, resulting in the formation of a pressure differential (negative ΔP).
To prevent this harmful ingress of dusty air, Cami has developed Ink-Jet Defender. The machine draws air from the environment outside the booth, with a flow rate calculated according to the range of observed cases. This air is filtered with a level of efficiency of F7-F9 and introduced into the compartment where the digital machine is installed. This creates a protective pressurisation (positive ΔP) consisting of air of controlled purity, which prevents the harmful ingress of dusty air.
The following are the main construction characteristics.
The Inkjet Defender 100 booth pressurisation system is an air treatment unit with a monobloc structure made of robust press-bent galvanised steel panels with interposed seals; it is equipped with counterframes for rapid insertion of filters, a filtering section with filter support frames and a soundproofed plenum to house the fan. The microfibre bag filters are sewn lengthwise and equipped with protective polyester coating. They have a nominal capacity of 2000 m3/h for the standard model, a filtering surface area of 6.8 m2 and a fine filtration class, level F7 or F9.
The high-performance electrical centrifugal discharge fan has the following nominal characteristics (model Inkjet Defender 100):
- Flowrate: 2000 m3/h;
- Installed Power: 1.1 kW;
- Power Consumption: 0.85 kW;
- Speed 2840 rpm and direct transmission.
The duct from the treatment unit to the booth has a cross-section sized to achieve the indicated air jet speed. Made of galvanised steel or stainless steel on request, it features low-pressure-drop fittings and segmented elbows treated with an internal sound-insulating coating for a low-noise airflow of suitable height and direction.
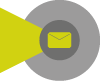
Did you find this article useful?
Join the CWW community to receive the most important news from the global ceramic industry every two weeks