Madirex of Manfredini e Schianchi
Building on its half century of experience in the field of dry grinding and granulation and treatment of the resultant powders, Manfredini & Schianchi has developed a new granulation system called Madirex which overcomes the limitations of conventional solutions. Depending on the particle size distribution of the incoming body, whether for standard single firing or for porcelain tile obtained with MS-Drytech Porcelain technology, Madirex agglomerates the power to the ideal particle size and humidity necessary to obtain the same level of flowability in the mould cavity as that of the spray dried powder. The granules are produced by the combined action of the circulatory movement of the powder with the humidification stage.
This movement is performed using specially designed blades that transfer the powder onto a non-stick inclined surface to increase granulation without forming large lumps. Humidification is achieved by water nebulisation using special disks that supply the required humidity uniformly to all the particles in the powder.
The automatic adjustment of the water pressure and of the disk and blade speeds determines the ideal particle size distribution of the finished product, while automatic electronically controlled humidity regulation allows Madirex technology to perform perfect granulation, minimising the use of water and making the subsequent drying stage superfluous.
The resultant particle size distribution has a percentage of superfine powder of between 8% and 12%. This level not only does not affect flowability but is in fact necessary for suitable integration of the granules, which sinter perfectly during the pressing stage to allow for rapid de-airing and to create an extremely smooth and uniform body surface.
Madirex has a special self-cleaning internal lining that allows it to be used for different bodies and different colours. The system does not require routine maintenance and reduces electricity consumption by more than 80% compared to conventional granulators.
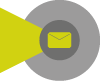
Did you find this article useful?
Join the CWW community to receive the most important news from the global ceramic industry every two weeks