Tecnargilla Preview - Sacmi presents a range of unique machines
Two years after launching the H.E.RO. project (High Efficiency Resource Optimizer), Sacmi will be back at Tecnargilla 2010 with a range of unique machines take advantage of new market trends, with an increased focus on energy saving and environmental protection.
Visitors and potential customers will be able to admire 3 firing modules of the new Eko Series single-layer roller kiln. This new kiln represents a real technological revolution, and incorporates systems for managing fume/product heat exchange, selecting which fumes to purify (fume volume per hour being significantly reduced in any case), and varying kiln length to suit production volumes. Eko kilns consist of a series of thermal modules or cells in which combustion fumes exchange thermal energy with passing material in a far more efficient manner than in traditional kilns. Eko kilns not only reduce the volume of toxic fumes that need to be filtered but, for the first time ever, allow different fume types to be identified and small volumes of specific fumes subjected to targeted purification to remove contaminants, with obvious benefits in terms of process simplification and respect for the environment. The use of cells enables the firing curve to be controlled more accurately while also allowing stable pressures and temperatures to be maintained even if the volume of tiles passing through varies. If the volume of production falls, the cells that are no longer needed can simply be deactivated: this amounts to having a variable-length kiln. Eko kilns are equipped with self-recovering burners which extract hot fumes from the kiln chamber and use them to heat combustion air (700°C) in counter-current.
Sacmi have also introduced significant innovations in pressing in the form of the new PH3200 press (32,000 kN pressing force, 2450 mm clearance). This is the first in a new range of presses featuring an innovative preload system based on alloy tie rods, combining the reliability of alloy with the simplicity of traditional tie rods The press structure has been designed using the latest optimisation software to limit stress and ensure greater reliability and increased rigidity (giving more uniform pressing). The new hydraulic system is equipped with sophisticated adjustments and controls to allow even the most difficult materials to be pressed, and new autodiagnostic software allows faults to be identified quickly. The new press is also equipped with the innovative DCL2450 powder loading carriage.
Another major development lies in the area of continuous grinding. This is the new L Cube (Long Life Lining) anti-wear mill lining made from vulcanised rubber coated alumina bricks, developed in collaboration with Bitossi and B & B. L CUBE gives a 5% higher output for the same energy consumption, and the lining lasts at least three times longer than traditional types.
Also on display will be the DDD175 digital decoration system, specially developed by Sacmi for controlled powder applications on ceramic substrates, with no limitations on particle size, moisture and colour. The system combines the flexibility of digital technology with freedom to use conventional and typical materials. It consists of a series of independent decoration units, one for each colour, located in sequence on a conveyor belt. By using data from a graphic management program to coordinate the various units, the complete decoration can be applied to the material as it advances along the line.
Finally, innovations in automatic handling and end-of-line automation will also be on display. Sima will be exhibiting its own machines for storing unfired ware in roller boxes and for stacking fired products on pallets, capable of working with larger sizes than ever before, as well as state-of-the-art laser guided vehicles. Nuova Fima will be exhibiting an automatic sorting and palletizing line suitable for the production of formats up to 1200 x 1500 mm, with fully automatic and computerised format change, equipped with all the necessary accessories for handling and packaging products of these dimensions. Surface Inspection will be exhibiting a new machine for 1200 x 1500 format, using advanced software to identify more defects than ever, even in the digital decorations that are becoming increasingly popular. And Sacmi will be showcasing its Sidepack packaging system. This new system drastically reduces the use of packaging material (which is often thrown away on building sites), thereby offering financial and environmental benefits to manufacturers and users alike. The new packaging machine uses the simple principle of protecting the corners and edges and is capable of packaging even slabs as large as 3 meters in length.
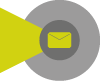
Did you find this article useful?
Join the CWW community to receive the most important news from the global ceramic industry every two weeks