Aliplast and Mirage team up on plastic waste recovery project
Aliplast and Mirage have developed a circular process for recovering plastic films used to package ceramic tiles.
Mirage, a renowned high-end Italian ceramic tile producer based in Pavullo in the province of Modena, has reaffirmed its longstanding commitment to sustainability. Its efforts are not limited to reducing the environmental impact of its products and production processes, but also focus on packaging.
In cooperation with Aliplast, part of Hera Group company Herambiente, Mirage recently initiated a circular process for the recovery of plastic films used in ceramic tile packaging.
Aliplast is not only a leading producer of flexible PE film, PET sheet and regenerated polymers but also has extensive experience in the ceramic sector, where it covers about 67% of the Italian market thanks to its wide range of solutions for recovering, recycling and regenerating plastic film.
A closed-loop process in the ceramic industry: how it works
The first step in the Aliplast plastic film recovery process adopted by Mirage involves sorting and compacting the waste material, an operation that takes place directly at the Mirage site. The material is then sent to the Aliplast hub, where it is reconverted into granules and subsequently into new packaging film ready for reuse in the Mirage production cycle.
The recovery process is based on the closed-loop principle aimed at ensuring maximum sustainability. This involves collecting plastic waste from companies and then processing and regenerating it to produce a high-quality material with comparable technical properties to those of virgin material and ready for reintroduction into the production cycle.
Assigning an objective value to sustainability
The Italian ceramic industry is increasingly embracing green principles, for which purpose it is important to know the precise extent to which a product or process contributes to reducing environmental impact. Objectively quantifying savings has always been one of the main aims of Aliplast, which for several years has been monitoring the greenhouse gas emissions associated with its five product types: PE granules, PE films, PET granules, PET sheets and PET flakes. In accordance with the LCA (Life Cycle Assessment) methodology, Aliplast evaluates the environmental impact of its products over their entire life cycle in order to obtain an objective measurement of the extent to which they contribute to reducing emissions, including their carbon footprint.
Aliplast methodology and data
One key metric that is widely used in life cycle assessments is CO2 equivalent, calculated using the IPCC 2013 GWP 100 methodology.
Analysis of Aliplast’s operations reveals that by producing approximately 100,000 tonnes of recycled products annually, the company avoids around 170,000 tonnes of CO2 equivalent emissions each year (2022 figures).
This is equivalent to more than 400,000 barrels of oil. In practical terms, choosing Aliplast’s recycled products enables suppliers and customers to reduce their greenhouse gas emissions by a volume comparable to around 100,000 petrol-powered cars travelling 10,000 kilometres a year.
The results of the partnership with Mirage
Each year, Aliplast supplies Mirage with more than 500 tonnes of Reload shrink film, a trademark for Aliplast products containing an extremely high percentage of recycled material, typically more than 80%.
The use of this type of material avoids approximately 1,200 tonnes of greenhouse gas emissions annually. Furthermore, by collecting and repurposing customers’ waste materials, Aliplast avoids sending these materials to landfill, thus embracing circular economy principles and enhancing environmental sustainability.
In short, the partnership between Aliplast and Mirage not only focuses on supplying suitable packaging materials but also translates into tangible environmental savings.




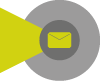
Did you find this article useful?
Join the CWW community to receive the most important news from the global ceramic industry every two weeks