Ancora supplies new slab finishing plant to Polialc

The new plant will perform surface lapping of glazed surfaces and polishing of full-body, double-loaded or through-vein unglazed surfaces on sizes ranging from 1000x1000 mm through to 1800x3600 mm and thicknesses from 5 mm to 30 mm.
Polialc, a Castellón, Spain-based company specialising in ceramic surface finishing and treatment and other services for the ceramic industry, has once again chosen Italian technology from Ancora for its new production facility.
After collaborating with the SITI B&T Group member company for its production line dedicated to traditional tile sizes, Polialc has placed another order with Ancora for its new slab processing and treatment department. Ancora’s technicians, in close collaboration with their colleagues at Polialc, designed a system for large sizes that would meet the evolving needs of the dynamic Spanish ceramic tile market and cater for a wide range of different sizes and thicknesses.
The plant is designed to work with sizes ranging from 1000x1000 mm through to 1800x3600 mm and thicknesses from 5 mm to 30 mm and performs surface lapping (semi-polishing) of glazed surfaces and polishing of full-body, double-loaded or through-vein unglazed surfaces.
- Flexibility and efficiency
A unique feature of this plant is its ability to produce both semi-finished and finished slabs by performing a grinding stage with an independent loading and unloading line. This means that Polialc can perform pre-grinding and polishing operations on one large slab while at the same time performing grinding on another slab on a parallel and completely independent line. With this degree of flexibility, Polialc can respond rapidly to any request from the Spanish ceramic market.
- Pre-grinding
In the first stage, the plant pre-grinds the edges of the slabs to prepare them for lapping. The purpose of this preliminary operation is to improve the efficiency and productivity of the lapping stage by defining the slab geometry with high precision and creating bevels on the sides and corners, thereby protecting the metal tools and avoiding the risk of scratching due to grit residues during lapping.
- Surface roughing
In the case of unglazed full-body porcelain, the system supplied by Ancora to Polialc also performs surface roughing, which involves using rigid tools to enhance the double loading, vein or grain effects. This machine consists of a single base with a swinging beam capable of machining the entire width of the slab (between 1000 mm and 1800 mm).
- Lapping
The lapping stage involves the use of two double beam lapping machines. Designed to handle ceramic tiles or slabs in thicknesses ranging from 5 to 30 mm, these two hi-tech machines feature all the solutions necessary to work on very different surfaces in terms of flatness, weight and thickness. The brushless motor and the oscillating beams for the edges of the slab help the operator choose the method and length of time for performing the critical edge lapping operation according to the type of slab. One of the key features of Ancora lapping machines is the option of choosing the type of tool according to the slab composition. Magnesium tools can be chosen for polished slabs or resin-coated tools for full-field lapped surfaces.
- Pickling
Pickling is a cleaning operation performed subsequent to lapping in the case of glazed surfaces and involves altering the glaze morphology. Also known as acid etching, this step is an integral part of the ceramic treatment process and is essential for making the lapped surface resistant to acid attack. Because of its porosity, the surface retains processing impurities if pickling is not performed. The process serves to neutralise these pores and remove any lapping residues.
- Porosity protection
The Ancora technology used in this step of the end-of-line process is called Hi-Coat. It is a highly versatile machine equipped with multiple independent heads which use soft tools to apply pore-filling products onto the surface of the slab, after which the pores are sealed with a protective acid-resistant treatment. The result is a uniform, durable surface with a high degree of resistance to the most common and stubborn stains.
- Grinding and checks
The grinding stage also uses sophisticated hi-tech machines to process large size slabs. The operator can control all operations via a remote-control system, which allows him to perform rapid and efficient size changes and to check grinding wheel wear and the general condition of the machine. Calibre and colour control are the final steps in the process before SITI B&T loading/unloading machines place the finished slabs in special boxes or racks for storage.
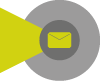
Did you find this article useful?
Join the CWW community to receive the most important news from the global ceramic industry every two weeks