The Belden Brick Company embraces digital decoration
The leading U.S. brick manufacturer is completing a major revamp at its Sugarcreek (OH) plant #8 that includes the adoption of digital printing and next-generation automation.

The Belden Brick Company, the largest family-owned and managed brick manufacturer in the United States, is finalizing a major upgrade program at its Plant 8 in Sugarcreek, Ohio, which involved the introduction of new technologies and automation, including two next-generation digital printers for brick decoration supplied by Projecta (B&T Group). Numerous factors have driven the big investment ($44 million) particularly the commitment to innovation and the desire to elevate the quality of our products. The company is known for its expertise in custom blends, sizes, colours, textures and historical restorations.
Cosmec is one of your key technology partners:
"Since we began the renovation of Plant 8 in 2018, Cosmec has been by our side, supporting us with cutting-edge solutions, including a new static dryer, two extrusion and cutting lines for bricks and pavers, an extrusion and cutting line for special pieces, automatic loading/unloading and handling of the dryer cars, a stacking machine, and all handling equipment for the two decorating lines, which will most likely be operational by May 2025. The automation will significantly reduce manual labour and, consequently, operating costs" said the CEO Robert Belden.
The production due to begin in 2025, the year of Belden Brick’s 140th anniversary:
“Family involvement and commitment have been the backbone of our longevity, along with our commitment to ensuring the sustainability of our products and processes” - the CEO continues.
The company has in fact implemented several measures about sustainability: the raw materials are locally, and the company embrace lean manufacturing principles to reduce waste and enhance efficiency throughout our production processes (the recycling of both green and fired brick waste is an examples).
In the future growth plans the company will fire up a roller hearth kiln which significantly enhancing the capacity to produce full-sized glazed brick and millions more thin brick. Another significant initiative will involve centralizing the raw material preparation and storage. Should demand continue to outpace supply, we are ready to activate our eighth tunnel kiln, currently undergoing repairs.
Read the full interview published in Brick World Review 1/2025
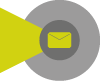
Did you find this article useful?
Join the CWW community to receive the most important news from the global ceramic industry every two weeks