In India, Motto has started up a new Sacmi Continua+ line
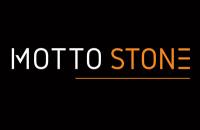
The Indian tile manufacturer has chosen a PCR 2000, as well as a new kiln and dryers with advanced heat recovery systems for ‘zero fuel’ performance.
Market-leading Indian ceramic tile company Motto has just installed and started up a new complete line for the production of slabs and sub-sizes. At its heart lies a Sacmi Continua+ with a PCR 2000 – the best-selling solution in the Continua+ family and the second such machine to be sold in India – for porcelain tiles as large as 1600x3200 mm and thicknesses from 6 to 20 mm.
Fully operational since early May at the plant in Morbi, this latest plant stands out for the choice of machines and solutions of unrivalled technology that result in ultra-high finished product quality and process efficiency.
Alongside the PCR 2000 (equipped with two APB powder feeders, which can be augmented over time, and a TPV unfired material cutting unit), Sacmi has also supplied a 45.2 meter 5-tier EM5 dryer and a pre-kiln dryer, both designed for completely ‘zero fuel’ operation thanks to systems that retrieve heat from the kiln (RVE).
The plant also includes a latest-generation 201-meter-long FCC kiln equipped with a very advanced energy saving system to minimize specific consumption and ensure a steady flow of heat to the dryers.
“The immediate result”, points out Motto’s owner, “has been a drop in both costs and consumption, accompanied by an increase in the quantity of first-class products”, thus meeting all customer’s objectives.
Beside boosting its ability to penetrate the high end of the market, Motto will also be able to manage in a versatile, efficient way the sizes in its portfolio, such as 1200x1800 and 1200x2400 mm slabs, thanks to the integrated unfired/fired material cutting solutions.
The plant was up and running in record time. This was the result of close collaboration between the two technical teams and Sacmi’s ability to send technicians to the site and monitor every single stage of installation and testing.
All the production tests were performed with raw materials and bodies already at the customer’s disposal.
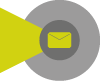
Did you find this article useful?
Join the CWW community to receive the most important news from the global ceramic industry every two weeks