Marcheluzzo Ceramics redesigns the drying process for Mladost
The innovative MT80evo internal chamber ventilation cone, which was designed and developed by the R&D department, has been successfully installed
Mladost, a leading Serbian clay brick manufacturer based in Vlasotince, approached Marcheluzzo Ceramics with a request to reduce the energy consumption of the dryer installed about 30 years ago. The Vicenza-based company took up the challenge by supplying an innovative MT80evo internal chamber ventilation cone, which was designed and developed by the R&D department and is already in operation at the customer’s facility.
Brick producers are well aware of the importance of powerful and uniform internal ventilation during the drying phase for the purposes of drying time, product quality and waste percentage. Nonuniform ventilation in either longitudinal or transversal directions results in uneven shrinkage of the material in the dryer. Parts exposed to a higher air flow or excessively high air velocities will tend to contract more rapidly than those that are shaded, potentially resulting in brick breakage. Thanks to the different aerodynamic solutions, the MT80evo ensures that air is distributed at a constant speed over all the material being dried, while its special geometry means it can be installed close to the roof of the dryer. This makes it possible to fully exploit the internal working height of the dryer chamber, which must be at least 21 cm from the top of the dryer in order to avoid severe losses that would reduce aerodynamic efficiency and result in nonuniform air currents.
Marcheluzzo devoted special attention to the quality and durability of the class H motors, which are oversized by 30% and are suitable for use in extreme humidity and temperature conditions. Maintenance work on the internal ventilation system has been reduced by 80% compared to traditional cones, while the main focus of the project was to reduce energy consumption. The new generation MT80evo cones have an installed power of 2.2 kW and allow for a very quick return on the investment (normally one year).
The system is the ideal solution for converting all low air efficiency chamber dryers so as to achieve greater productivity, higher quality and significantly reduced consumption.
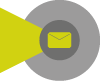
Did you find this article useful?
Join the CWW community to receive the most important news from the global ceramic industry every two weeks