Reco2, a new answer to the energy saving
Sacmi has recently added to its long list of innovations for the sanitaryware sector with the introduction of a new brand, Reco2, presented for the very first time at Tecnargilla - the trade fair dedicated to technology and systems for the ceramics industry. Reco2 promises to be the reference standard for all new projects carried out by the Sacmi Group's Whiteware Division.
There are several key aspects to the Reco2 concept, each of which derive from the experience and successes achieved by Sacmi through working on important projects such as, for example, the supply made to the state-of-the art Ceramica Catalano factory in Italy. First and foremost are the machine technical specifications which allow for very considerable savings, minimization of energy consumption and reduction of polluting emissions.
In fact Sacmi is convinced that energy saving provides not just an economical advantage but also, especially in the long run, represents significant added value for manufacturers who are obliged to adjust to ever stricter standards on reduction of emissions.
First to break new ground and attract a positive response from the market have been the new shuttle kilns with Reco burners and tunnel kilns with EMS (Energy Management System), provided with an air pre-heating chamber and an energy recovery system. These innovative machines are the result of experience acquired by the Sacmi Group through its sister company Riedhammer and which combine energy efficiency with the reliability and attention to quality that have long been the hallmarks of Riedhammer's products and services.
This kind of technological efficiency perfectly matches Sacmi's system solutions which provide pre-drying stations enabling the energy consumption of the production line to be further reduced while, at the same time, improving health and safety in the workplace.
With Sacmi's plants customers can count on a reduction in production cycle times of 40%, in storage space requirements of 30% and in total energy costs of the complete pre-drying and drying process of up to 50%. Furthermore, the presence in glazing booths of innovative dry filters provides for the elimination of waste water and, therefore, treatment costs.
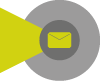
Did you find this article useful?
Join the CWW community to receive the most important news from the global ceramic industry every two weeks