Sabo and Ladrillos Fortes still in partnership with Sabo
The recent supply of a complete turnkey plant strengthens the partnership started in 2014 between the two companies.

In 2014, Sabo signed an agreement with Ladrillos Fortes to supply a new turnkey plant in the city of Lima, Peru. The goal of the project was to achieve a production capacity of 500 tonnes per day of all the different bricks and hollow blocks found on the Peruvian market.
The success of the project marked the beginning of a longstanding professional partnership between the two companies based on mutual trust.
Ladrillos Fortes, one of Peru’s largest brick manufacturers with four facilities located throughout the country, subsequently chose Sabo to supply technology for three more projects. One of these projects involved upgrading the Trujillo plant in northern Peru, where Sabo supplied a modern cutting and loading line capable of loading products directly onto the kiln cars without passing through a dryer.
Ladrillos Fortes requested a plant capable of producing 500 tonnes of bricks and blocks per day, including Techo 15, Techo 12, Panderreta and King Kong. Furthermore, the line had to be able to process Techo 15 and Techo 12 blocks in both horizontal and vertical formats.
The plant proposed by Sabo included a slug pre-cutter, followed by a robust side cutter that could work with both stiff and wet extrusion. The cutter was fitted with a double harp, allowing the line to work continuously without stopping even in the event of a wire breakage. This harp has the ability to move aside automatically, allowing a new harp to take its place immediately. This enables the cutter to continue operating without having to stop and wait for the broken wires to be replaced.
A Fanuc robot with a loading capacity of 700 kg was installed for kiln car loading. The automation included the latest programming bench, which Sabo has used in many different projects in the USA and Latin America in the last 4-5 years to allow clients to work with many different bricks and formats. A drag and separation system with a completely new design were also added with the aim of avoiding any kind of mark or wear on the bricks.
Sabo placed significant emphasis on safety measures, incorporating fences, light beams and access control. This reflects its commitment to operator safety as a fundamental requirement for any project, regardless of its location worldwide.
The results of the project fully satisfied the customer’s requirements, testifying to the Sabo team’s high level of professionalism and dependability.
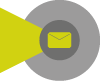
Did you find this article useful?
Join the CWW community to receive the most important news from the global ceramic industry every two weeks