The Sicer solution for production flexibility and consistent quality

While Full Digital is without question the ultimate goal, it is important to manage the change by developing a mentality that combines ceramic expertise with a knowledge of the specific aspects of the digital process.
By Sergio Marcaccioli, Sicer (Fiorano, Italy)
Production trends in the ceramic sector are evolving constantly and growing ever more complex.
Whereas in the past the ceramic tile industry was characterised by large production batches and mass deliveries, the situation today is very different with manufacturers making increasingly specific and ad hoc requests. Both now and in the immediate future, production processes must be able to meet requests for small batches (1500 m2) of extremely high quality products (95%) within very short timeframes. This means changing product type several times per day on a given production line, which creates greater difficulties in terms of set-up and error minimisation.
The fact that ceramic is now used in the furnishing segment for products such as bathroom and kitchen countertops has further increased the required quality criteria and reduced the margin for error.
In this scenario, glaze and colour producers play an increasingly strategic role for ceramic companies and a strong partnership between the two parties is the only valid solution.
With this in mind, Sicer is not just a supplier but acts as a full-scale partner for its customers. Only by establishing close collaboration and teamwork is it possible to provide dedicated customised solutions that guarantee research, innovation and consistent quality.
One example of the excellent results achieved through this process of continuous technological improvement is the development of new ceramic bodies and substrates. Rather than just simple structural bases, these materials now serve as a starting point for creating specific aesthetic effects (white, super-white and bleached bodies, coloured bodies, porcelain bodies, etc.). With its in-depth technological knowledge of the type of body and of the technical characteristics of the glazing line and kiln, Sicer is able to offer a customised package that the ceramic producer company can elaborate and personalise.
One of the tile manufacturers’ key goals is to stand out and make themselves immediately recognisable in the market, which they can achieve by conducting research into material surfaces and delivering stress-free products with excellent chemical and physical characteristics and good levels of transparency in the case of polished materials. Sicer is able to measure and study these parameters thanks to the important investments in cutting-edge technological instrumentation it has made in recent years and its policy of expanding its team of laboratory staff with both experienced professionals and freshly graduated technicians.
For ceramic glaze and colour producers, research results in a high degree of fragmentation of offerings and products, while the situation is made even more complex by the pressure of on-demand deliveries and the limited planning allowed by the market. In a scenario where it is no longer sufficient simply to supply compliant materials, it is clear that only real collaboration with customers can provide a basis for lasting and mutually beneficial relationships.
The development of digital printing technologies has brought excellent results, including expanded colour gamut and depth, flexibility, application of multiple digital materials (glossy, matt, metallized), full-field and non-full-field digital glue, etc. Scope for adding decorative effects has been expanded, along with the increased consistency of application and consequently perceived value. At the same time, however, it has reduced the potential for differentiating products and brands. While Full Digital is without question the ultimate goal, it is important to manage the change by developing a mentality that combines ceramic expertise with a knowledge of the specific aspects of the digital process. A number of key aspects must be taken into consideration, including the fact that improving production efficiency is not always a successful strategy whereas increasing the percentage of first choice products is always beneficial, so all possible measures must be taken to achieve this.
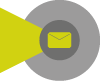
Did you find this article useful?
Join the CWW community to receive the most important news from the global ceramic industry every two weeks