Tile cooling system "Igloo Cube 3.0" by Tekmak
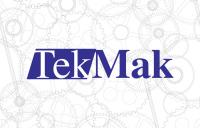
In 2012 Tekmak became the first company in the world to develop a patented system, called Igloo, for cooling tiles entering digital printers. In 2014 it developed version 2.0, the Igloo Combo system. To date around 200 Igloo devices in the two versions have been installed in 26 different countries. Tekmak has continued its research efforts in this field and the company is now presenting version 3.0, Igloo Cube, the most innovative and revolutionary version in terms of energy consumption, dimensions and performance.
Igloo Cube cools tiles prior to digital printing so as to eliminate a high percentage of the moisture present in the glaze applied to the ceramic body and to significantly lower the glaze temperature, thereby creating the ideal conditions for any type of digital printer. Igloo Cube is based on direct exchange cooling technology. It is an extremely compact machine with very small dimensions (1460x1700 mm and a height of just 1400 mm), allowing it to be installed along any glazing line – even those that are very short and equipped with large numbers of accessories. The machine is installed on the glazing line without the need to interrupt operation. It is mounted on its own supporting frame, leaving the section below the conveyor belt clear.
The direct exchange system is extremely efficient thanks to theuse of full inverter technology, which allows for significant savings compared to similar machines (up to three times lower levels of consumption). With an installed power of just 11 kW, the machine has a minimum consumption of just 2 kW/h and an average hourly consumption of just 6 kW/h, the lowest of any kind of cooler.
Tekmak’s experience in the construction of coolers over the last 4 years has enabled it to make optimal use of the small installed capacity by exploiting extremely high cooling efficiency and using the patented Vortex AirFlow system to block steam production. In practice, special airflow geometries are used to produce air vortices at temperatures below 0°C, which strike the tile at close range and at speeds of more than 120 km/h. This freezes the surface of the tile, preventing steam from flowing from the tile body to the digital printheads. The fact that the glaze is cold and dry allows the digital printer to perform problem-free printing. The effect lasts for just a few seconds, the time needed for the tile to pass underneath the digital printheads.
Igloo Cube is also equipped with an ultra-rapid cleaning system that enables the machine to be fully cleaned in a couple of minutes without the need for operator intervention. Because Igloo Cube is connected to the digital printer by means of an electrical contact, the cleaning operations of the two devices are synchronised so the glazing line never needs to be stopped.
The new Tekmak machine is designed not just for conventional size tiles but also for large panels and extra-thick slabs. A dedicated electrical system with video camera can be installed to maintain the ideal distance between the tile and the air vortex outlet according to the thickness of the tile. If tiles of different size and thickness are decorated on the same line, the air vortex will always have the same ideal impact distance.
Igloo Combo is the first cooler built with a master/slave system, making it particularly suitable for the production of large panels. A tunnel of length 3,200 mm (or even 4,800 mm) can be created using the control panel commands of the Siemens PLC system installed on the Master machine and simply fitting the machine with the necessary modules.
The new cooler improves print quality and increases printhead lifetime by keeping them clean and efficient and allowing for smoother production without machine downtime. At the same time it has the lowest operating costs of any technology in existence.
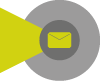
Did you find this article useful?
Join the CWW community to receive the most important news from the global ceramic industry every two weeks