TOP Squadra Dry by BMR
The dry grinding technique has been successfully used with monoporosa and porcelain tiles for a number of years now. And thanks to BMR’s unflagging R&D efforts, the dry squaring process can now be applied to porcelain surfaces using the new TOP Squadra Dry squaring machine.
To be able to use this process with porcelain tiles and panels, a number of conditions must be met. These include dedicated tools, a slightly lower speed compared to wet grinding, a larger number of calibrators (12) and the use of a sleeve filter to collect process dust. At the same time it brings a number of major advantages for users: the absence of water in the department, the elimination of foundations and the need for a water recycling system, a longer lifetime of parts over the entire grinding line and the possibility of recycling ground raw material.
Just as with monoporosa tiles, the dry grinding process adopted with porcelain involves pulverising the removed material. The squaring machine is equipped with a casing and ducts for the removal of grinding dust. The spindle casings are provided with special devices to control the extraction flow according to the working speed and the characteristics of the raw material dust.
Two kinds of grinding wheels can be used according to the type of porcelain: resinoid or metallic. These have a special diamond coating for dry grinding and a bond with high thermal conductivity.
The pusher, a vital component for the geometric quality of the squaring operation, consists of two arms, one of which is motorised and encoder controlled and can be reset from the operator keyboard to guarantee the tile’s diagonal dimension.
The squaring machine can be connected to a dimensional electronic control system for fully automatic diagonal checking and recovery.
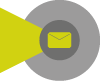
Did you find this article useful?
Join the CWW community to receive the most important news from the global ceramic industry every two weeks