Altadia Group: The hydrogen route to decarbonisation
As part of the H2frit project, the first pilot test of a hydrogen-powered kiln for ceramic frit production is now underway at the Esmalglass-Itaca facility in Villareal.

On 14 October, Esmalglass-Itaca (part of the Altadia Group) welcomed the partners in the H2frit project to its facilities in Villareal (Castellón) to see first-hand the results of the first pilot test of a hydrogen-powered ceramic frit kiln.
Promoted by the Spanish ceramic frit, glaze and colour producers’ association ANFFECC and financed by the Generalitat Valenciana, the H2frit pilot project, entitled Decarbonisation of the ceramic frit sector through the use of hydrogen in the melting process for the production of ceramic frits, was approved last October by the Ministry of Industry of the Generalitat Valenciana. The project aims to assess the technical feasibility of replacing natural gas with hydrogen as a fuel for ceramic frit melting, thereby supporting the sector’s efforts toward decarbonisation.
The three-year project involves the collaboration of a consortium of leading companies consisting of bp, Carburos Metálicos, ITC - Institute of Ceramic Technology and Grupo Altadia.
During the first few months, the project focused on developing engineering plans to adapt the production process to the use of hydrogen, as well as designing the skids, burner and control panel. The testing methodology was also chosen and frits and refractory materials selected for analysis. Following extensive technical and organisational coordination by ANFFECC, the hydrogen plant was successfully installed last June at the frit plant operated by Esmalglass-Itaca, the ANFFECC member company where the research work will be carried out.
In addition to the two bays housing the external hydrogen storage and refuelling platforms, the installed equipment includes control panels and connection and supply pipes complete with pressure accessories (valves, regulators, etc.) designed by Carburos Metálicos (Air Products Group).
Testing will take place in a pilot oxyfuel kiln, concentrating on the technological adjustments required for the use of hydrogen.
Technical consulting on hydrogen use and supply is provided by bp, while ITC-AICE has performed preliminary tests in a controlled-atmosphere kiln to examine the impact of different hydrogen and natural gas mixtures on the frit melting process.
During testing, hydrogen will be introduced in different percentages to determine the necessary technical adjustments and assess their feasibility with the aim of maximising hydrogen use in frit production and significantly reducing CO₂ emissions into the atmosphere.
During the visit to the plant, Esmalglass-Itaca CEO Manuel Sanz thanked the partners for their hard work and collaboration in a pioneering project that seeks to steer the ceramic frit, glaze and colour industry towards a more sustainable future.
“As Esmalglass-Itaca and Grupo Altadia, we are very proud to host this first pilot test at our facilities and to actively contribute to the decarbonisation of the industry in line with European Union targets,” said Sanz. “Projects like this are essential for progressing towards a sustainable and environmentally friendly industry.”
Nonetheless, there is an awareness within ANFFECC that alongside hydrogen, “there are other alternatives that could contribute to the decarbonisation of the sector and which will also need to be studied”.
Grupo Altadia’s roadmap towards decarbonisation
Esmalglass-Itaca’s participation in the H2frit project fits in perfectly with the Altadia Group’s decarbonisation plan aimed at achieving zero emissions by 2050, an ambitious roadmap involving an initial investment of over €7 million.
The short-term goals include a 14% reduction in emissions by 2025 compared to 2021 levels, increasing to 37% by 2030.
The plan also includes installing 24,000 photovoltaic panels on the roofs of Esmalglass, Itaca and Fritta’s four factories, which will meet over 18% of their electricity needs and avoid approximately 3,000 tonnes of CO2 emissions annually, the equivalent of preserving around 2,000 hectares of woodland.
The H2Frit project may also prove pivotal for the company, enabling it to extend oxyfuel technology to additional plants in the future, depending on technology and fuel supply availability.
As part of its product research efforts, the Spanish group has introduced Slim Body, a complete solution for producing low-thickness tiles that cuts gas consumption by 15% and reduces emissions by 12%, while also boosting productivity by 30%.
Altadia Group’s ongoing commitment to environmental, economic and social sustainability is reflected in the certifications it has obtained in the past year and a half, with Esmalglass-Itaca attaining ISO 45001 (health and safety) certification and Younexa achieving both ISO 45001 and ISO 14001 (environmental management) certifications. As a result, Altadia is now the first group in the sector with all three certifications – ISO 9001, 14001 and 45001 – across all its Spanish factories.
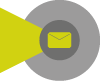
Did you find this article useful?
Join the CWW community to receive the most important news from the global ceramic industry every two weeks