Ceramica Cerrad invests in Sacmi technology
Sacmi has been commissioned to supervise renovation and extension of the plant in Starachowice, Poland of Cerrad, a longstanding manufacturer of pressed clinker. The fully automated installed line has complex and ambitious characteristics and offers plenty of margin for energy saving. This was a real challenge for Sacmi, which for the project adopted the finest technology available on the market.
The heart of the system is the double layer kiln which achieves a total tile output of 12,000 sq.m/day and allows for a high degree of manufacturing flexibility. The upper channel is used to produce medium-large floor tiles while the lower one simultaneously produces 245x65 mm trims (7,000 sq.m/day or more than 300 pieces per minute). The process occurs directly from the presses and output is sorted and packaged automatically. Two PH3200 hydraulic presses with an inter-column clearance of 2,450 mm, capable of pressing 22 cavities for trims or medium-large floor tiles in a single row, were equipped with the brand-new CRS (rapid mould changeover) device, resulting in downtimes of less than thirty minutes and previously unseen levels of mould changeover manoeuvrability, accessibility and simplicity. Thanks to the short downtimes, the handling system for both unfired and fired materials is direct, with fixed one-hour storage boxes for both planned and unscheduled stops. Sima's engineers have come up with innovative and personalised solutions for the safe and secure management of production rates that can peak at 360 pieces/minute per channel. Four Nuova Fima sorting and packaging lines have been installed at the kiln outlet complete with all the devices needed to handle the difficult range of sizes. Sacmi Forni has also supplied two horizontal multi-channel ETP dryers in conjunction with the double layer FBN kiln, designed for efficient channel separation. The resultant specific gas savings are in the region of 30%.
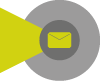
Did you find this article useful?
Join the CWW community to receive the most important news from the global ceramic industry every two weeks