Full Digital Glaze line from Durst proves a big success at Tecnargilla
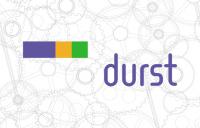
Durst Full Digital Glaze Line technology, the fully digital glazing line unveiled for the first time by the Bressanone-based company, was a big success at Tecnargilla 2016. Visitors to the company’s stand had the chance to observe step-by-step tile production using the full digital process, as well as a range of applications displayed in the Durst Glaze Gallery.
The result of 5 years of R&D efforts, the Full Digital Glaze Line is based on an open system. "This enables it to work with glazes from third party manufacturers that are very similar to those used with conventional systems while guaranteeing versatility, flexibility, high quality standards and extremely competitive management costs," explained Norbert von Aufschnaiter, Director of the Durst Ceramics Division.
The Full Digital Glaze Line synchronises the glazing, printing and finishing operations in keeping with a 4.0 vision of the manufacturing process. The line is built around the latest-generation Durst Gamma DG technology (for digital glazing and the creation of variable textures) and the new 8-colour inkjet printers from the Durst Gamma XD 4.0 series (for decorating applied textures and as a prerequisite for access to DG technology), all of which are managed in a single workflow.
The Durst Gamma DG 4.0 glazing system offers an efficient alternative to conventional methods. Starting out from a smooth mould, it is able to apply a full-coverage layer of glaze and create authentic textures with extremely high definition and relief in a thickness of up to approximately 1 mm. As well as giving the tile a material, tactile effect, the system also guarantees the maximum creativity in the production of different textures, such as reproductions of wood grain, stone, concrete and textiles.
This is achieved by using a patented proprietary printhead technology designed and developed by Durst to manage high viscosity water-based glazes with a particle size up to 45 microns or more at a speed of 20 linear metres a minute with a single glaze bar. The machine’s double colour bar configuration allows for the simultaneous application of two different glazes for effects that could not previously be achieved on the glazing line. When the bars are used individually, the one that is not in operation can be prepared for the subsequent job without interrupting the production process.
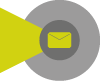
Did you find this article useful?
Join the CWW community to receive the most important news from the global ceramic industry every two weeks