Iris Ceramica Group and Edison Next produce the world’s first ceramic slab with green hydrogen
The test phase is underway for using a blend of green hydrogen and natural gas at the H2 Factory to verify that the technical characteristics and quality of the slabs remain unchanged.
Iris Ceramica Group, world leader in the production of high-end technical ceramic slabs, and Edison Next (part of Edison Group) announce the production of the world’s first 4D technical ceramic slab using a blend of green hydrogen (obtained using renewable energy) and natural gas.
Specifically, the slab produced is 3.2 metres long, 1.6 metres wide and 12 mm thick, and stands out for its four dimensions, thus the name 4D Ceramics: In addition to the three-dimensionality of the material and its grains, crossing the whole thickness of the slab, the fourth dimension is sustainability.
The slab has been produced at the Iris Ceramica Group’s H2 Factory, the new plant in Castellarano, (province of Reggio Emilia), which was completed in 2023 and already equipped with the innovative technologies and infrastructures needed to use 100% green hydrogen.
The industrial process being developed in Castellarano is the first concrete result in the process of decarbonising the ceramics industry that Iris Ceramica Group and Edison Next are working on jointly.
After this initial phase, the H2 Factory will be powered by higher percentages of green hydrogen produced in a cutting-edge, bespoke plant already designed and being implemented by Edison Next.
“The start of this phase is a concrete step towards net zero for a particularly energy-intensive industrial sector like ceramics”, Giovanni Brianza CEO of Edison Next stated. “This is the proof that, by putting technologies and innovation into play alongside skill and determination, we can achieve major results even in fields where this challenge is tough, as it demands the rethinking of the whole production process and the use of more forward-looking technologies like hydrogen. We are proud to be working with one of the top names in Italian manufacturing on this pioneering initiative, not only for the whole sector but also for the country, supporting a new industrial culture that focuses on sustainability. This is not only an opportunity for positive change but also a tool for increasing competitiveness in the reference markets.”
“Today marks a major achievement, yet another tangible fact that bears witness to our commitment to decarbonising the ceramics sector”, Federica Minozzi, CEO of Iris Ceramica Group said. “This is a unique and pioneering project with world-wide scope that offers new prospects for hard-to-abate manufacturing, showing that it can be done”.
As Federica Minozzi has explained, the test phase will help to fine tune the production process, before moving on to the next phase, which will allow to increase the percentage of green hydrogen more and more, up to 50% with the bespoke production system that Edison Next is creating for Iris Ceramica Group.
“This is a highly valuable partnership – Minozzi added -, and we are proud of this achievement, the result of teamwork within the whole supply chain and a virtuous example of integrated sustainability. We hope that other companies will follow our path, so that we can work as a system and become a driver of change, both nationally and beyond”.
The first phase of the project
Several preparatory activities have been completed in order to launch this first phase: the civil works
to prepare the area, the installation of the blending unit, which is the system that mixes the natural gas with the green hydrogen, and all the connections required between the different equipment.
Furthermore, a 1.3 MWp1 photovoltaic system has been installed, in addition to the existing 2.5 MWp plant.
In particular, the H2 pilot production plant, in operation since May 2024 for the test phase, includes two temporary electrolysers with a total power of 120 KW, powered by renewable energy. The two electrolysers, installed in a container, can produce up to 20 cubic metres of green hydrogen per hour, powering the new, latest-generation “hydrogen ready” kiln with a blend of green hydrogen up to around 7%; this percentage will increase once the final plant is installed.
The aim of this first phase is to study the use of the technology for the production of ceramic slabs using green hydrogen and, at the same time, verify the behaviour of the material during the firing phase, in order to be able to industrialise the production with green hydrogen with the certainty of assuring the technical and aesthetic excellence and quality that Iris Ceramica Group has always guaranteed.
In parallel to the test phase, in the coming months Edison Next will start all the activities required to install the final system, a plant producing green hydrogen through electrolysis with a capacity of 1 MW and able to produce around 132 tonnes of green hydrogen a year, which will be used to power the kiln with a blend of methane and green hydrogen up to around 50%.
The blend will immediately replace around 500,000 cubic metres of natural gas per year, avoiding around 900 tonnes a year of atmospheric emissions of CO2.
The green hydrogen production system being implemented by Edison Next is already designed to double the production of green hydrogen, which will be able to feed a new 100% hydrogen kiln currently under study.

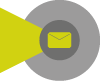
Did you find this article useful?
Join the CWW community to receive the most important news from the global ceramic industry every two weeks