Italgraniti adopts the first PCR 2120 from Sacmi
The latest addition to the Continua+ family has been installed at the Italgraniti factory in San Martino in Rio (Reggio Emilia)
Italgraniti, one of Italy’s leading producers of ceramic tiles and slabs operating under the Italgraniti, Impronta and Italston brand names, is the first company to adopt Sacmi’s PCR 2120, the latest addition to the Continua+ family which was recently launched onto the market.
This willingness to invest in new process technologies is nothing new for the ceramic group, which was founded in 1994 and worked together with Sacmi to pioneer the development of the first Continua technology. “In 2002 Italgraniti came up with the idea for a revolutionary technology involving continuous compaction of a spray dried powder bed based on the Cotto Calvetro extrusion process which was then in use at our Rubiera factory. We subsequently developed this technology in cooperation with Sacmi’s technicians and engineers,” says CEO Francesco Maturo.
The market has changed enormously in the intervening 20 years and Italgraniti’s latest investment in its facility in San Martino in Rio (Reggio Emilia) aims to eliminate the need for a warehouse entirely. “We have to be increasingly prepared to operate on a work-to-order basis so as to respond rapidly to market requests without sacrificing productivity, efficiency or line saturation,” says Maturo. This makes it necessary to manage small batches, different sizes and the hundreds of different products in the catalogue, all with the same levels of efficiency.
“This is why we chose the PCR 2120,” explains Maturo. “This innovative solution combines all the recognised advantages of the Continua+ technology, including superior quality and versatile size changeovers, with those of a traditional press such as productivity, cost control and use of the same bodies.”
The first advantage of the PCR 2120 compactor is its ability to work with tiles and not just slabs, while maintaining the same levels of quality and efficiency.
“On the one hand, we need to schedule very different orders and very small production batches without being constrained by size changeover times or the minimum efficient size needed to saturate a traditional press line,” adds Maturo. “On the other, we need to guarantee perfect process quality and repeatability across the various tile sizes that are often used within a single architectural project.”
As well as the ability to work with the same body regardless of size, the PCR 2120 also guarantees the same colour tone and texture across the entire batch, with perfectly repeatable results every time.
Further advantages include shorter set-up times and the possibility of increasing the number of sizes being produced thanks to integration with unfired and fired cutting solutions. More specifically, each individual size produced in the compactor results in at least four separate but identical sizes.
The efficiency of Continua+ is also reflected in the production of minimal quantities of waste regardless of size and the possibility of recycling the waste entirely within the process, as Italgraniti is already doing. “Last but not least, this machine has just over a third of the installed kilowatts of a standard solution,” adds Maturo.
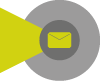
Did you find this article useful?
Join the CWW community to receive the most important news from the global ceramic industry every two weeks