Kajaria adopts Sacmi Continua+ technology and enters the large slab segment
This spring the Indian group will be starting up a new PCR2120, the smartest machine in the Sacmi Continua+ line-up, together with a 5-tier dryer and a kiln equipped with Sacmi’s latest energy efficiency solutions
Kajaria Ceramics, India’s top tile manufacturer and the seventh largest producer in the world, is about to complete another major investment. The new PCR2120, the latest addition to the Sacmi Continua+ line-up, is due to come on stream this spring at the Tirupati plant, one of the Group’s ten production sites in India, and will enable the well-known ceramic brand to enter the premium ceramic slabs and surfaces segment. Kajaria has invested constantly in innovation and service throughout its more than 33 years of history and is now the leading brand in the Indian market and a major exporter to Europe and the USA.
“Technology, research, quality and design have been part of Kajaria’s DNA ever since it was founded,” says Chairman Ashok Kajaria, who now runs the company together with his sons Chetan and Rishi. “We have always adopted the latest available technologies with a view to improving the quality and appeal of our products and the efficiency of our factories.”
The PCR2120 is designed specifically to produce the most popular sizes on the market, from 60x120 cm to 120x240 cm together with the corresponding sub-sizes, and is extremely compact and versatile, largely due to the integrated TPV on-the-fly cutting system supplied by BMR. As a result, it is a valid alternative to even the highest performance traditional presses. Equipped with upstream APB0 and DMS feeders, when fully operational the machine will be capable of producing 3.5 million square metres per year in the various sizes and thicknesses. It will have a specific consumption of just 0.06 kWh per square metre (compared to an installed power of 80 kW) and scrap levels below 3%, regardless of the product size.
Kajaria also commissioned Sacmi to supply the thermal machines for its new Tirupati plant: a 5-tier dryer with a useful width of 2850 mm and length of 47.6 metres, the 25.3-metre pre-kiln and the new 210-metre HTE295 kiln, a latest-generation machine fully equipped with systems for recovering hot air from the kiln and sending it to the burner preheating area and dryer. This investment reflects the efforts made by the Indian ceramic industry to respond to the problem of soaring energy prices by adopting advanced energy efficiency solutions capable of improving the energy balance of its factories.
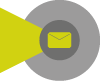
Did you find this article useful?
Join the CWW community to receive the most important news from the global ceramic industry every two weeks