New standards in brick slip production
Innovative Sacmi/BMR technology flies to the United Kingdom for one of the country’s top brick manufacturers.

As it prepares to launch brick slip production, one of the UK’s leading brick manufacturers has chosen innovative Sacmi/BMR technology.
Specifically, the British company has adopted Sacmi’s exclusive extrusion system, which eliminates the traditional cutting process and brings significant advantages in terms of sustainability, energy savings, waste reduction and overall process optimisation.
To complete the new plant, BMR’s Brick Division has supplied two machining lines for rectifying, side cutting and edging brick slips and mech slips. At the heart of the supply package is Squadra Kerf, the latest innovation from the Italian company, designed to ensure high precision, superior quality and increased overall efficiency. This precise, efficient and sustainable solution improves the process by minimising reworking and waste. BMR’s Brick Division specialises in advanced technologies for the brick industry, offering cutting-edge solutions for edge grinding and chamfering.
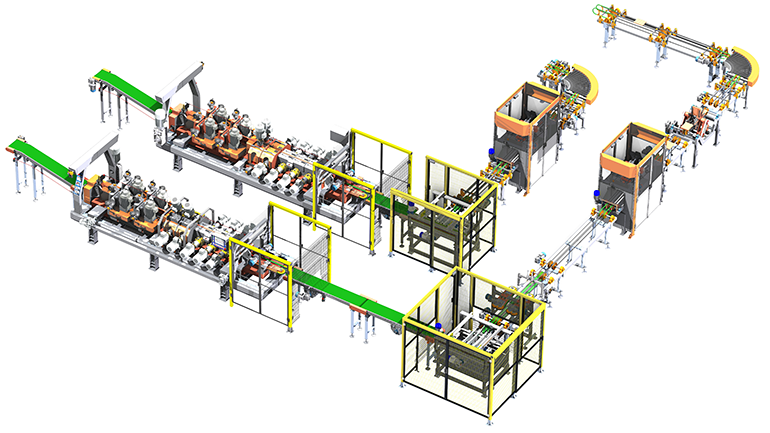
Squadra Kerf: repeatable quality, sustainability and efficiency
Squadra Kerf is a high-precision solution with a robust steel frame, ideal for dry grinding brick slips using opposing side cuts. The material is handled by an advanced mechanically-synchronised toothed belt system driven by an inverter-controlled gear motor, moving along hardened steel guides to ensure consistent performance and long-term reliability.
To maintain stability during the machining operation, the machine features a cushioned upper pressing unit, where the thrust force is regulated by a system of pneumatic cylinders and balancing rods, allowing it to adapt constantly to production requirements.
One of the key strengths of Squadra Kerf is its machining head system, which guarantees high-precision machining at every stage. For front calibration, the machine is equipped with six opposing heads with electric spindles, whose speed can be controlled via inverter. It also features four variable-position heads which can be used for both front calibration and side cutting. Each unit operates on dedicated sliding guides.
For side cutting operations, the machine features four opposing cutting heads mounted on a double slide system with recirculating ball guides, allowing for precise adjustment along both the horizontal and vertical axes.
In addition to its mechanical performance, Squadra Kerf also stands out for its new dust management system. The machine is equipped with an extraction system that locates the strategic extraction points, thereby minimising residual dust dispersion. This results in a cleaner process, enhancing both the long-term quality and reliability of machine operation and workplace health and safety. All machine parameters are controlled via an integrated PLC, ensuring real-time process monitoring.
BMR partners the brick industry in the green transition
The adoption of BMR technology is driven by the need to produce high-quality finished products while minimising waste and energy consumption. The supply of these two state-of-the-art lines marks a crucial phase in the UK company’s plant conversion project, which is due to begin in the next few months.
The company’s goal is not only to meet the growing demand for this type of product but also to pursue an increasingly sustainable manufacturing approach. The decision to adopt BMR’s innovative technology to eliminate traditional cutting marks an important step in this direction.
The entire brick industry is watching this ambitious project closely, as it has the potential to set new standards for the entire sector, with BMR emerging as a key partner in driving sustainable transformation.
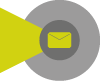
Did you find this article useful?
Join the CWW community to receive the most important news from the global ceramic industry every two weeks