Sacmi Heavy Clay cements its position in Argentina
Sacmi Heavy Clay, a division of Sacmi Imola specialising in heavy clay technology, continues to consolidate its position in the Argentinian market by concluding the start-up test of an important project with one of the country's most prestigious clients. In conjunction with its programme to increase production capacity, Cerámica Fanelli S.A (a company based in La Plata, a province of Buenos Aires, which is part of the Later-Cer S.A group) acquired and successfully started production in the new plant extension that was necessary to achieve net volumes of 1,300 tons of heavy clay bricks per day.
The project provided for mechanical and electrical updates to the cutting line to adapt it to the new large-exit extrusion system, and to allow the new production rhythm to be adequately managed. The dryer car loading and unloading machines were also split in two, as had already been completed for the programming line for kiln car stacking, all of which was integrated into the new, high-concept management software. This software allows a wide range of products to be produced, with the management of format changes only requiring the pre-programmed setting on the operating panel. The installation serves a robot cell from Gaiotto Automation, a Sacmi Group company specialising in automations. The robot cell consists of two palletization robots able to bear a load of 700kg, mounted with clamps for picking up single layers from two sides, with variable axle-spacing for simple and efficient loading of the entire product range, including hollow and load-bearing bricks, floor and insulation blocks. In order to manage the new production quantity, equivalent to more than 25 drying cars/hour, Sacmi Forni were commissioned to create two twin transfer cars with variable axle-spacing for loading and unloading the dryer.
Sacmi Forni were also responsible for widening the continuous tunnel dryer, featuring a main thermal room and a recirculation circuit in the damp zone. Other features of the dryer include the creation of a high yield internal ventilation system via adjustable cones, which allow the air flow to be perfectly maintained from the kiln towards the products to be dried. The strong point of the diffuser cones lies in the use of modern fluid-dynamic analysis systems which allow a constant air speed to be maintained throughout the entire drying car. The movement of the adjustable cones is achieved via a high-quality, low-maintenance system, by means of an optimised continuous transmission system.
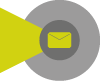
Did you find this article useful?
Join the CWW community to receive the most important news from the global ceramic industry every two weeks