Robatech: Hotmelt gluing systems adopt Industry 4.0 principles
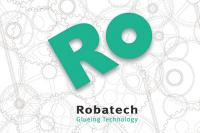
Davide Morten - Robatech Italia
Robatech, the world leader in the development and production of adhesive application systems, has applied principles of Industry 4.0 to its hotmelt gluing systems, opening up new frontiers in smart innovation. The result is a series of innovative equipment and technologies complete with interfaces that improve control, monitoring and maintenance of the packaging line.
Hotmelt systems for sealing packages are used in a wide range of industrial sectors and in the ceramic industry are used for gluing cardboard blanks, for coupling packs and for applying scratch-proof wax.
Robatech’s latest goal in the field of Industry 4.0 was to integrate the gluing units installed in end-of-line machines both physically and technologically for the first time ever. This involved applying advanced interfaces and control centres capable of communicating with a network of equipment, sensors and software.
The RobaVis Host software has been specially developed to offer plant manufacturers all the advantages of centralised control of Robatech equipment via the packaging line’s main control panel. In other words, RobaVis Host is a smart system that allows the adhesive application plant to communicate with the packaging line and thereby achieve real-time monitoring of the production process.
RobaVis Web marks a further step up from RobaVis Host. Unveiled at Interpack in May, it is the new web browser platform that allows all functions to be controlled remotely from a smartphone or tablet. Developed with a responsive design on a Windows platform, RobaVis Web can be used on any machine independently of its operating language.
Robatech is the only company in the world currently able to integrate its systems on packaging lines and has already adopted this high level of integration for leading companies. This has brought enormous advantages in terms of data measurement.
The innovative Infoplus software installed on hotmelt gluing systems enables various operating data to be collected, recorded, analysed and displayed in an easily comprehensible manner. Key measurements include glue and electricity consumption (hourly, daily and monthly), pneumatic and hydraulic pressure, adhesive temperature in the tank, pipes and guns, adhesive level in the tank using intelligent level sensors (ILS), and the pump and gun cycle count.
The data are transferred from the central unit to all devices by means of an ultra-fast real-time communication protocol. Robatech is the only company to provide communication modules compatible with Ethernet real-time Bus Communication systems (Ethercat, Ethernet Powerlink, Ethernet/IP, Modbus, ProfiNet, Sercos, Varan).
As well as responding immediately to processes, it is also possible to perform predictive maintenance by measuring parameters that identify the time remaining before planned maintenance, thereby cutting costs.
This brings numerous benefits for users, including real-time supervision of the entire gluing process with warning functions and considerable savings in energy and adhesive. This results in a significant improvement in efficiency, less waste and consequently a clear reduction in Total Cost of Ownership.
Swiss multinational Robatech is based in Muri and has been operating since 1975. It has approximately 580 employees working at subsidiaries and service and spare parts centres in 70 countries worldwide.
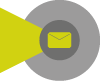
Did you find this article useful?
Join the CWW community to receive the most important news from the global ceramic industry every two weeks