Cerámica Rosario expands its drying department
Cosmec will install two new drying lines alongside the six existing lines, to achieve a daily production of 1,030 tonnes of hollow bricks,
Cerámica Rosario, based in the province of Santa Fe, Argentina, recently commissioned sophisticated technological solutions to expand its drying department. To do this, it once again turned to its longstanding supplier Cosmec, which it considered to have the right skills and expertise to improve the efficiency and performance of complex thermal machines. To achieve a daily production of 1,030 tonnes of hollow bricks, Cosmec will install two new drying lines alongside the six existing lines. The new drying tunnels will be equipped internally with mobile cone ventilation devices, with a galvanised steel double cone diffuser and an air distribution grille of the same height as the load to be dried.
This system ensures rapid and uniform drying and consequently eliminates the risk of internal stresses due to different drying speeds between different parts of the product, thereby reducing the quantity of waste and ensuring high quality standards.
The expansion project developed by Cosmec involves removing the infill masonry from the south wall of the dryer, repositioning the monodirectional conical diffusers belonging to the last line and adding new bi-directional devices between the supporting columns. The flow of hot air is supplied by centrifugal fans, while internal air recycling is performed by fans that take the moist air from the flues, mix it with ambient air, pre-heat it by means of auxiliary burners and introduce it into the initial section of the tunnel.
The moist air is extracted from the tunnels by means of axial fans installed on the tunnel ceiling in a rear position with respect to the entrance transfer table.
In order to speed up car movements inside the dryer, the decision was taken to modify the existing transfer tables and increase the loading capacity from one car to two cars. This was achieved by associating each existing transfer table (master) equipped with autonomous drive and centring device with a non-motorised “slave” transfer table capable of separating itself from the “master” unit and moving to the correct car loading or unloading position. The two drying lines are currently being assembled and will be commissioned in around June 2021.
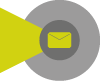
Did you find this article useful?
Join the CWW community to receive the most important news from the global ceramic industry every two weeks