Dry grinding gains in popularity in the Far East
After being adopted by Thai Ceramic in 2012 and Royal Ceramic in 2013, dry grinding technology from Manfredini & Schianchi is continuing to expand in Thailand. A raw materials plant delivered to Siam Ceramic of Saraburi, a member of the colossus SCG, came into operation in August.
The new line will meet the needs of a daily output of 35,000 sq.m of single fired floor tiles in sizes 30x30 cm, 40x40 cm, 50x50 cm and 60x60 cm. The plant features a P.I.G HD Dryer as the primary mill and a new Molomax 6/500 pendular mill for the refining stage. The Molomax mill can achieve a throughput of more than 30 ton/h with separation below 63 micron. This guarantees an extremely smooth, impurity-free finished product surface that is ideal for the use of digital technology and high-gloss glazes.
The agglomeration and powder humidification phase is performed by the Madirex 2400 granulator (patented worldwide), today considered the technological benchmark in dry milled powder granulation.
In spite of the past reluctance shown by the Southeast Asian market to adopt dry milling, further endorsement of MS-Drytech technology in the region has come from the leading Vietnamese firm Prime Group. Likewise part of the Thailand-based colossus SCG, it commissioned Manfredini & Schianchi to upgrade its current dry milling system supplied in 2009 in terms of quality and capacity.
The plant is equipped with three Molomax MS4/230 pendular mills, together with P.I.G-Dryer mills and Forgia MS38 granulators, and has a capacity of more than 93 tons/h of dry body. This guarantees a production of 80,000 sq.m/day of high-quality single fired tiles in sizes up to 60x60 cm. By adopting MS-Drytech technology together with good quality local raw materials, Prime Group has been able to reduce consumption of heat (-96%), electricity (-47%) and raw materials (-75%), maintenance costs (-36%) and atmospheric emissions of CO2 (-77%) compared to the wet milling process.
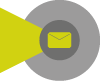
Did you find this article useful?
Join the CWW community to receive the most important news from the global ceramic industry every two weeks