La macinazione a secco convince anche il Far East
Dopo essere stata adottata da Thai Ceramic nel 2012 e Royal Ceramic nel 2013, la tecnologia di macinazione a secco di Manfredini e Schianchi continua a espandersi in Tailandia, dove in agosto è entrato in funzione l'impianto di preparazione materie prime fornito alla Siam Ceramic di Saraburi, parte del colosso SCG.
La nuova linea soddisferà una produzione giornaliera di 35.000 mq di pavimento in monocottura nei formati 30x30, 40x40, 50x50 e 60x60 cm. L'impianto si avvale del mulino P.I.G HD Dryer come macinatore primario e del nuovo mulino pendolare Molomax 6/500 per la fase di raffinazione; quest'ultimo è in grado di produrre oltre 30 ton/h con taglio di separazione inferiore a 63 micron per garantire una superficie del prodotto finale estremamente liscia, priva di impurità e quindi ideale per l'applicazione della tecnologia digitale e di smalti superlucidi.
La fase di agglomerazione e umidificazione polvere è affidata al granulatore Madirex 2400 (coperto da brevetto mondiale), ad oggi considerato il riferimento tecnologico nella granulazione per polvere macinata a secco.
Un'altra importante conferma della validità della tecnologia MS-Drytech anche per il mercato del Sud Est Asiatico, in passato particolarmente diffidente verso la macinazione a secco, è giunta dal leader vietnamita Prime Group, anch'esso parte del colosso tailandese SCG, che ha affidato a Manfredini & Schianchi l'upgrade, qualitativo e quantitativo, del suo attuale impianto di macinazione a secco fornito nel 2009.
L'impianto è dotato di tre mulini pendolari Molomax MS4/230, corredati di mulini P.I.G-Dryer e granulatori Forgia MS38, con una capacità di oltre 93 ton/h di impasto a secco che garantiscono una produzione di 80.000 mq/giorno con formati fino al 60x60 cm di monocottura di alta qualità. Rispetto alla macinazione a umido, la tecnologia MS-Drytech, unita anche alla buona qualità della materie prime locali, ha consentito a Prime Group di abbattere i consumi termici (-96%), elettrici (-47%) e di materie prime (-75%), i costi di manutenzione (-36%), nonché le emissione di CO2 in atmosfera (-77%).
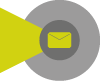
Hai trovato utile questo articolo?
Unisciti alla community di CWW per ricevere ogni 15 giorni le principali novità da tutto il mondo sul settore ceramico