Neolith doubles its production capacity with the new Sacmi FMA Maestro kiln
The start-up of the new kiln completes Neolith’s production expansion announced in 2021, doubling its capacity for 1600x3200 mm size slabs.
Neolith, the world’s leading producer of large sintered stone surfaces, has completed the industrial expansion project it announced a year ago, doubling the production capacity of its most popular large size product (1600x3200 mm) sold in more than 100 countries worldwide. To achieve this, the Spanish ceramic company has installed and started up a new FMA Maestro kiln from Sacmi, a longstanding technology partner which has previously supplied modular mills and spray dryers for the body preparation department.
Chosen as part of the company’s focus on sustainable growth and high value-added products, the new kiln features superior control solutions that allow for precise management of all phases, especially the critical cooling phase.
José Luis Ramón, CEO of the Neolith Group, believes it is essential “to have the best available technology, as this ensures we are able to satisfy the needs of architects, designers and end consumers. For this reason, adopting state-of-the-art technologies has been one of our top priorities and also enables us to optimise energy use, sustainability and corporate solidity. The Sacmi kiln is the best solution to our current needs.”
The new kiln, a 228.9-metre FMA 235, incorporates all the advantages of the Maestro range (a higher percentage of first-class products, lower levels of consumption and fewer unburnt residues) and is equipped with a new generation of high-performance burners. The kiln is specially designed for efficient control of large size slab firing and to ensure optimal management of the mechanical tensions that typically occur at the end of the firing process.
To distribute heat evenly over the entire surface and cross-section of the slab and ensure perfect flatness, Maestro features dual rapid-slow cooling with burners positioned underneath the roller planes and dedicated ceramic blowers for the centre and walls of the kiln. In addition, dedicated controls (e.g. automatic valves and blowers) allow users to set recipe-specific parameters to maximise flexibility and repeatability and ensure a rapid response to changes in operating conditions.
The FMA also features a modulated air-gas system that enables users to adjust the air-gas ratio in the various zones independently. Temperature control is performed by simultaneously adjusting air and gas flow rates, while the ratio between the two is adjusted mechanically. This means that for each group of burners the air-gas combustion ratio remains constant not only when the set temperature changes but also in the event of variations in load conditions, bringing clear advantages in terms of versatility and efficiency.
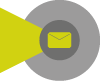
Did you find this article useful?
Join the CWW community to receive the most important news from the global ceramic industry every two weeks