Target net zero: Apulum rises to the challenge
The Rumanian tableware manufacturer has started up a new Sacmi spray-dryer ATM18 that will allow to carry out part of their spray-dried powder production vertically and to completely recycle scrap and waste within the line.

One of Europe’s largest tableware manufacturers and the market leader in Romania, Apulum Porcelain Factory has been operating since 1970 in Alba Iulia, the city built on the site of the Roman fort of Apulum and former capital of the Principality of Transylvania. Here, in a 160,000 square metre production facility, the company produces 50 million pieces/year, 90% of which are exported.
The company’s main markets are Europe and Mexico, but it also ships its products to Japan, South Korea, Hong Kong and North America, where they are sold by its biggest customer IKEA.
Apulum has seen steady growth and development in recent years, and posted revenues of €36 million in 2021. Its success owes much to the focus on innovation and the state-of-the-art technology introduced by the new owner, the Italian company Rody Time Italia led by Alvaro Santini and Rodica Vasin, which has been the majority shareholder since 2007. In particular, the company has made significant investments in process automation and digitalisation.
“The use of robotics enables even the most complex product formats to be produced and finished to perfection, significantly reducing the percentage of waste and making the process more efficient and aligned with our sustainability goals,” the company said.
As Apulum’s main technology supplier since 2010, Sacmi is supporting the company through its process of expansion and upgrading, which now includes a focus on the circular economy and a zero-impact future.

Target zero waste
A Sacmi ATM18 spray dryer designed specifically for tableware body production was recently installed at the Alba Iulia plant and will enable Apulum to internalise and verticalise part of its granulate production and recycle process waste totally in-line, reusing it as a raw material. The goal is to fully recycle green scrap and waste (and fired scrap after grinding) in the spray dryer. This farsighted project was agreed on in December 2021, well before the international situation regarding energy prices and raw materials procurement became so critical.
The machine has an evaporating capacity of 1,000 litres/hour and is capable of producing approximately 1.6 tonnes/hour of spray-dried powder (the precise quantity depends on the standard moisture content of the slip entering the machine and the required residual moisture content percentage of the output, which varies between 2% and 3% according to the recipe). Although it does not entirely meet Apulum’s current production requirements, the machine marks the first step towards the adoption of a circular economy policy aimed at reducing the company’s environmental footprint, minimising its reliance on resources and lowering its procurement costs.
Sustainability and efficiency are further enhanced by the design of the spray dryer, which combines an independent lance spraying system (a total of 7 lances, each with 2 nozzles) with solutions for dust and fume abatement by means of cyclones and wet filters compliant with current emissions standards and regulations.
The project involved close cooperation between Sacmi and Apulum’s technical teams, from the infrastructure work (the roof was adapted prior to installing the machine) to auxiliary equipment and steelwork. Sacmi also supplied systems allowing the spray dryer to be fully integrated with the existing body preparation line.
Greater efficiency, less waste
The project follows on from Apulum’s previous investments in Sacmi technology. In 2021 the Romanian company completed the purchase of a new Sacmi-Sama isostatic press (PHO Green), the sixth such solution installed since 2015, along with a Nebula airless glazing system suited to single-fire tableware production. Along with their high efficiency, both solutions make a significant contribution to environmental sustainability. The PHO451 Green press allows for up to 30% savings in energy and raw material consumption, while Nebula uses dedicated systems to capture vapourised glaze and completely reintroduce it into the process, thereby avoiding waste and the risk of contaminating the workplace.
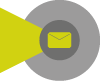
Did you find this article useful?
Join the CWW community to receive the most important news from the global ceramic industry every two weeks