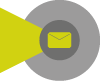
Be the first to know!
Get the most useful and interesting news from the global ceramic industry in your inbox every two weeks
Recent articles
Ceramica Sant’Agostino goes for SACMI Continua+
Jul 15, 2025
Guocera invests in large slab production
Jul 14, 2025
Ceramic World Review 162/2025
Jul 11, 2025
China’s tile industry and market continue to decline
Jul 11, 2025
Chinese tile exports fall to 600 million sqm
Jul 11, 2025