Digital technology and ceramics: a winning combination
System Ceramics continues on the path of innovation and takes stock of the latest developments and ongoing research in the field of digital decoration: from the digital application of grits with Infinity Dry to the new Infinity Sky platform, in anticipation of the transition to Full Digital.
The digitalization of the ceramic process is now an absolutely winning path, it is an axiom.
System Ceramics’ experience in this field has been equally successful, marked by continuous technological progress through collaboration with customers and ink producers. The company has participated in numerous R&D projects without excluding any type of ink. These efforts culminated in the development of water-based inks, a major breakthrough that became a reality with the first production lines launching in 2024. This strong synergy among all ceramic industry players, combined with seamless integration across System Ceramics’ multidisciplinary R&D teams (covering electrical, chemical, physical, mechanical and software engineering), has contributed significantly to the company’s success. Today, System Ceramics is the undisputed global leader in digital printing machines with a substantial installed base worldwide.
The new Infinity Sky platform
Continuing its tradition of innovation, System Ceramics unveiled a preview of its new project, Infinity Sky, at Tecna 2024, with the new digital decoration platform due to be commercially available by the end of this year. Building on the success of the Infinity printer – already known for its exceptional quality – Infinity Sky incorporates several key improvements specifically requested by customers and ink manufacturers.
To ensure maximum flexibility, Infinity Sky can accommodate up to 16 positions for loading colours and materials. Each of these 16 bars is independently configurable and features a pneumatic lifting system, which hermetically seals any unused bar for enhanced protection.
The machine also features an advanced automatic maintenance system. When the bars are in standby mode, they remain in a dynamic rather than static state to ensure optimal readiness for use. This is achieved through an ink recirculation inversion system that preserves printhead functionality. Additionally, Infinity Sky enhances reverse recirculation by integrating an ultrasonic generation system within each bar, exploiting the unique properties of piezoelectric printheads. This innovation significantly extends the duration of print quality while enhancing the lifespan of all circuit components.
All these innovations contribute to making Infinity Sky a more sustainable solution, optimising both the machine and the overall process. It is compatible with all available ink types and eliminates material wastage.
Infinity Dry

With the Infinity Dry System platform, System Ceramics has also digitalised the powder application process. Starting from the highly successful and innovative Genesis patent, the company has adapted a fully pneumatic printhead to selectively deposit grits (glassy powders). Since powders have their own unique rheology, the printhead was specially modified to ensure optimal fluidisation and application.
The key advantage of this method is its precision. Infinity Dry deposits exactly the required amount of grit precisely where needed, according to the desired graphic pattern. This targeted deposition process ensures accuracy, minimises material waste and reduces production costs.
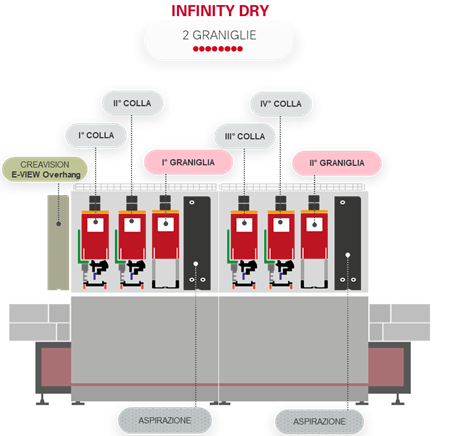
Full Digital
The final step towards fully digital ceramic decoration is digital glazing, a concept that has been discussed for years and is now nearing practical implementation. However, digital glazing is currently limited to certain specialised production lines and predominantly uses submicron materials. This means there is still considerable room for technological innovation and the development of new machines in this field.
System Ceramics’ research efforts aim to apply materials with larger particle sizes – certainly greater than a micron – to enhance the material’s body and deliver the improved mechanical strength and performance characteristics associated with larger particle sizes.
Another important goal is to increase discharge capacity. Current digital machines are able to deposit up to 100 grams per square metre at speeds of around 20 m/minute, whereas the next step will involve selectively depositing even larger quantities for both full-field applications and digital designs, allowing for the creation of micro and macrostructures directly on ceramic surfaces.
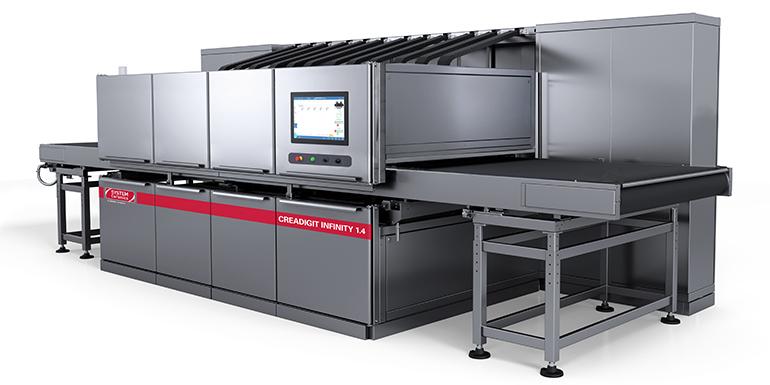
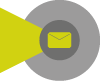
Did you find this article useful?
Join the CWW community to receive the most important news from the global ceramic industry every two weeks