Equipceramic: efficient management of extremely high factory temperatures
Equipceramic has developed a new tunnel kiln featuring a special insulation/cooling system designed to reduce the temperatures inside brick and roof tile factories.

One of the biggest challenges facing brick manufacturers in hot climates is managing the extremely high temperatures reached inside factories during production. Due to its high internal temperatures of approximately 1,000ºC and its extensive radiating surface, the kiln is the most significant single source of heat. This makes it essential to devote special attention to the design of the kiln’s insulation system and cooling circuit.
Equipceramic has developed a new tunnel kiln featuring a special insulation/cooling system designed to reduce the temperatures inside brick and roof tile factories. The goal is to keep operational temperatures below 50°C, the highest permitted workplace temperature in many countries.
A cooler energy-efficient kiln
In a recent project, Equipceramic successfully maintained the kiln’s exterior wall temperature at 50ºC, just 5ºC higher than the ambient temperature of 45ºC. This solution also reduced energy consumption compared to a conventional kiln. In general, adding extra insulation to the kiln walls is not on its own sufficient as it requires an excessive increase in thickness and results in prohibitively high construction costs.
In this project, an in-depth study of suitable insulation was complemented by the adoption of an air cooling circuit to achieve the desired temperature reduction.
The air used to cool the kiln walls is collected by means of manifolds and then fed into the kiln via the air-burner circuit, resulting in significant energy savings. In addition, a powerful cooling circuit installed beneath the factory roof helps to cool the kiln ceiling and also channels cooling air directly into the dryer.
A new concept in dryer ventilation
The dryer is another major source of heat, but in this case a different solution was adopted to that of the kiln. This involved improving the wall and ceiling insulation by adopting sandwich and spray foam solutions while also introducing an innovative ventilation concept – undoubtedly one of the most interesting aspects of the project.
The dryer, a semi-continuous model equipped with cone-shaped air recirculation fans, offers a number of advantages over conventional semi-continuous dryers, including a 40% reduction in dryer car width, a 40% increase in the number of fans and a 40% increase in the air flow rate.
The introduction of these three measures allows for improved air circulation around the products being dried, shorter drying times and – most importantly – the potential to operate at lower temperatures. This in turn leads to an automatic reduction in the dryer’s internal wall temperatures. Combined with the enhanced insulation of the external walls, this solution is able to achieve a temperature differential of less than 5°C between ambient temperature and the dryer’s external walls.
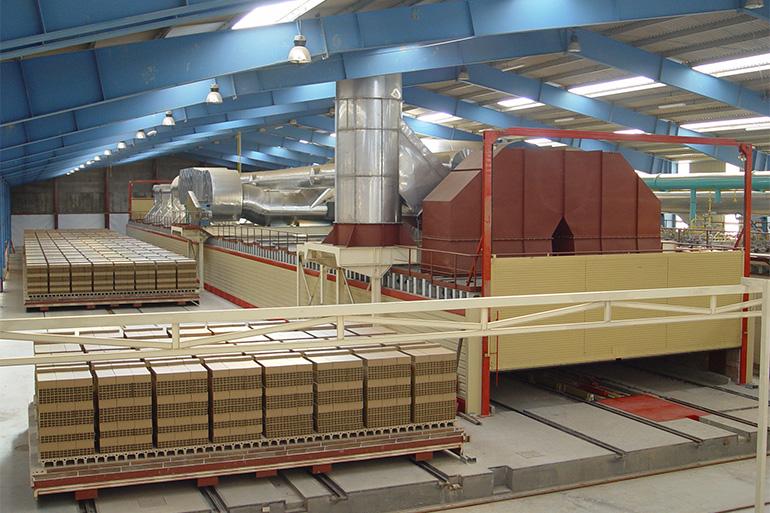
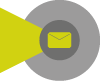
Did you find this article useful?
Join the CWW community to receive the most important news from the global ceramic industry every two weeks