Ipeg
The principle underlying this new firing technology is the development and use of special variable flame speed burners. These burners are able to create a perfect temperature distribution across the width of the kiln by controlling the combustion product outlet speed and temperature as well as the combustion product trajectories, which can be pre-set and modulated.
As a result, the kiln can be managed in a zero or negative pressure environment, thereby allowing for the total elimination of visible ceramic fibres, considered a health hazard. The kiln also cuts down workplace pollution caused by pollutants that develop in the firing channel and originate from the ceramic material and from combustion products. At the same time the intake of parasite air is reduced by more than 80%. This has been achieved by using a specially designed and patented adjustable sealing system which uses a compensation chamber located between the inner channel and the outer environment. This system is totally reliable in the case of negative pressure in the firing channel.

This has made it possible to develop air recycling systems and to use oxidising mixes of air and fumes at high temperatures as the combustion fluid for the new burners, thus saving roughly 30% on energy consumption.
Due to the need to collect and recycle air inside the kiln, it was necessary to conduct a detailed study of the kiln's interior environment to ensure that it did not contain special pollutants. On the basis of the results of the study, modifications were made to the adjustment stage so as to be able to collect air from the kiln environment, in the zone where the temperature is slightly lower than 500°C (pre-heating) and 700°C (cooling), thereby achieving extremely high energy savings.
By collecting air at temperatures of just under 500°C (pre-heating zone), it has been possible to carry though a project to eliminate VOCs (Volatile Organic Compounds), which until now have not been treated due to the high cost of introducing a post-combustion system for installation onto the fume chimney. To reduce these polluting emissions, the traditional kiln has been redesigned with a new kiln section in which the fumes originating during firing are physically separated from those developed in the first areas of the kiln containing the VOCs.
The VOCs are then treated in special post-combustion radiating burners. The need to keep post-combustion parameters constantly under control has led to the development (in conjunction with the La Sapienza University in Rome) of a prototype for on-line pollutant control based on a photothermal deflection laser technique.
Technical characteristics:
- productivity: 12,000 sq.m/day;
- product type: red body, size: 330x330x8 mm, cycle: 30 min.;
- energy consumption: < 400kcal/kg;
- elimination of ceramic fibres;
- parasite air reduction: > 80%;
- reduction of VOC and aldehyde emissions: > 90%.
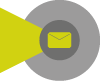
Did you find this article useful?
Join the CWW community to receive the most important news from the global ceramic industry every two weeks
Recent articles
Genitec supplies its technology to Morocco
Jul 17, 2025
Ceramica Sant’Agostino goes for SACMI Continua+
Jul 15, 2025
Guocera invests in large slab production
Jul 14, 2025
Ceramic World Review 162/2025
Jul 11, 2025