Alla base di questo nuovo concetto di cottura ci sono lo sviluppo e l'impiego di speciali bruciatori a velocità di fiamma variabile, in grado di creare nella sezione del forno una perfetta distribuzione della temperatura grazie al controllo della velocità, della temperatura dei prodotti di combustione e delle loro traiettorie predeterminabili e modulabili.
La conseguenza pratica è una gestione del forno in regime di pressione nulla, o di depressione, che ha reso possibile la completa eliminazione delle fibre ceramiche in vista, ritenute pericolose per la salute, e la riduzione dell'inquinamento dell'ambiente di lavoro causato della fuoriuscita degli inquinanti che si sviluppano nel canale di cottura e provenienti dal materiale ceramico e dai prodotti della combustione, riducendo anche di oltre l'80 % l'ingresso di aria parassita. E' stato infatti messo a punto e brevettato un sistema di tenuta regolabile, tramite camera di compensazione tra canale interno ed ambiente, di assoluta affidabilità nel caso di gestione in depressione del canale di cottura.

Questo ha reso possibile realizzare ricicli di aria e utilizzare miscele ossidanti di aria/fumi ad alta temperatura, come fluido comburente per i nuovi bruciatori, con la riduzione dei consumi energetici dell'ordine del 30%. La necessità di operare prelievi e ricicli di volumi all'interno del forno ha richiesto uno studio approfondito dell'ambiente interno del forno, per evitare la presenza di particolari inquinanti. I risultati ottenuti hanno permesso di intervenire in fase di regolazione per potere procedere a prelievi realizzati nell'ambiente "forno", nella zona di temperatura di poco inferiore ai 500° C in preriscaldo ed ai 700° C in raffreddamento, per ottenere elevatissimi risparmi energetici.
La possibilità di potere operare prelievi a temperature di poco inferiori ai 500°C in preriscaldo ha portato alla realizzazione di un progetto per l'abbattimento delle SOV (Sostanze Organiche Volatili), che ad oggi non vengono trattate a causa del costo elevato che deriverebbe dall'introduzione di un sistema di postcombustione al camino fumi. Per l'abbattimento di tali emissioni inquinanti si è riprogettato il forno tradizionale, sviluppando una nuova sezione di forno in cui si separano fisicamente i fumi provenienti dalla cottura, da quelli che si sviluppano nelle prime zone del forno, contenenti le SOV, trattando questi ultimi in idonei bruciatori radianti postcombustori. La necessità di tenere costantemente sotto controllo i parametri della postcombustione ha condotto a realizzare, in collaborazione con l'Università La Sapienza di Roma, un prototipo per il controllo on-line degli inquinanti, basato su una tecnica laser di "deflessione fototermica".
I dati tecnici:
- produttività: 12.000 mq/giorno;
- tipologia produttiva: pasta rossa, formato: 330x330x8 mm, ciclo: 30 min.;
- consumi energetici: minore 400kcal/kg;
- eliminazione delle fibre ceramiche;
- riduzione dell'aria parassita: maggiore 80%;
- abbattimento delle emissioni di SOV e aldeidi: maggiore 90%.
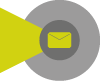
Hai trovato utile questo articolo?
Unisciti alla community di CWW per ricevere ogni 15 giorni le principali novità da tutto il mondo sul settore ceramico
Articoli recenti
Genitec porta la sua tecnologia in Marocco
17/07/2025
Guocera investe sulle grandi lastre
14/07/2025
Ceramic World Review 162/2025
11/07/2025