Marcheluzzo upgrades Fornace Vizzolese’s production line
The Vicenza-based company has made the existing production line more flexible and efficient with a new generation of automation and robotic systems.
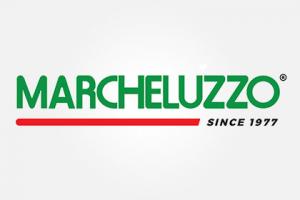
For several years now, Marcheluzzo has been dedicated to providing its customers with solutions capable of upgrading obsolete plants that are no longer aligned with market demands and integrating them seamlessly and sustainably into the production environment
Modernising a specific section of an existing production plant by introducing next-generation automation benefits the entire production line, improving its flexibility and efficiency for a relatively modest investment. This upgrade process restores the functionality of machinery and equipment that might otherwise have been taken out of service and potentially scrapped. This is the concept behind the recent order fulfilled by Marcheluzzo for Fornace Vizzolese, a well-established Italian company situated on the outskirts of Milan and led by Luigi Emilio Besozzi, his sister Maria and his two children Filippo and Laura, who are poised to assume leadership of the company in the near future.
Using robotics to improve process efficiency
In his role as head of plant operations, Filippo Besozzi approached Marcheluzzo with a request to modernise the outdated and uneconomical cutting, product handling and loading area using robotic systems. This complex task required a thorough examination of the production environment in order to make the most effective changes and improvements.
In response, Marcheluzzo devised a new integrated cutting line featuring 4 harp cutters capable of performing various types of cuts: 55 mm, 120/240 mm, 190 mm and 250 mm.
“The enormous flexibility of the line allows us to handle multiple formats, thereby enhancing productivity and meeting market demands,” notes Filippo Besozzi.
The cutter’s base is securely anchored to the floor and designed to facilitate the replacement of solely the upper section where the wires are located.
The cutter is followed by a spreading table equipped with a pantograph device which automatically arranges the pieces with the correct spacing ready for the subsequent drying process.
The entire green product handling process is performed with the aid of toothed belts, which are suitably sized to manage the load and ensure precise movement.
Metal rollers are entirely absent from the conveyor line and, most importantly for the customer, the entire handling and preparation line is engineered to prevent pieces from toppling over, even when handling narrower pieces alongside wider ones.
Different types of products are programmed according to their shape and size and are subsequently picked up by a robot equipped with three different types of grippers tailored to the products’ specific requirements.
In late 2022 and early 2023, Marcheluzzo began assembling the new machinery in close collaboration with the customer. The system was commissioned and tested towards the end of March.
Sustainability of the investments
Energy efficiency, waste reuse, and CO2 emission reduction are unquestionably top priorities. However, to truly embrace a circular economy, it is crucial to also focus on the repurposing of existing equipment. As a result, plant manufacturers are increasingly being asked to find ways to retrofit outdated production lines and thereby make processes more efficient.
“When considering the sustainability of investments, it is important to bear in mind that customers are increasingly requesting plant modifications that salvage as much of their existing equipment as possible. These interventions use modern technology to improve product quality, reduce energy consumption and, most importantly, enable operators to work with greater efficiency and safety,” explains CEO Paolo Marcheluzzo.
For several years now, Marcheluzzo has been dedicated to providing its customers with solutions capable of upgrading obsolete plants that are no longer aligned with market demands and integrating them seamlessly and sustainably into the production environment. An increasing number of companies are requesting solutions for upgrading the drying/firing areas, optimising energy consumption or even automating specific process stages rather than replacing the complete line. These solutions result in significant cost savings in terms of both operational expenses and initial investments.
“These interventions are often complex and require in-depth knowledge of company processes,” adds Paolo Marcheluzzo. “One of our greatest satisfactions is seeing our customers improve their competitiveness and efficiency while rapidly recouping their investments.”





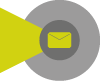
Did you find this article useful?
Join the CWW community to receive the most important news from the global ceramic industry every two weeks