The reconditioning of worn out moulds takes time and effort and costs money. Martinelli Ettore's "Long Life" range is designed to reduce these problems and extend the working life of universal bases, moulds and master moulds beyond one year on the press.
The HW range of wear resistant liners, which can last for over 2 million pressing cycles without loss of shape, has now been extended by the introduction of a new model for top forming moulds.
A specially developed and perfected formula of high temperature sintered powders ensures constant quality and tile dimensions over time, and limits wear to the top and bottom punches.
The new H-LIFE liners, designed for use in forming tiles with rounded corners and wavy sides, complete the range. These liners are made from top quality materials and are specially treated to resist wear. Their use can double the length of time for which all types of mould can be used, while also solving the problem of the ceramic body sticking to the liner.
Two accessories in abrasion resistant steel extend the working life of the master moulds: Dura-Frame shields and Dura-Strip listels protect master mould surfaces against wear caused by the sliding action of the loading carriage. A simple anchoring system and reduced weight allow these accessories to be replaced directly on the press. Their use allows master moulds to maintain their original height, and prevents loading precision being reduced by scoring of the profiles.
Dustop, a dust-proof bellows made entirely from long-life polyurethane, can support significant levels of stress and high operating temperatures for periods in excess of a year, and provides complete dust protection for the area of contact between the ejector and the base plate.
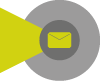
Did you find this article useful?
Join the CWW community to receive the most important news from the global ceramic industry every two weeks