System Ceramics: 4Phases for solving current warehouse management problems
Ever since the development in 1976 of the first Wrap Around system, which subsequently became a standard for the end-of-line stage, System has led innovation in the field of ceramic packaging. The company is now proposing 4Phases, a completely revolutionary system that solves current warehouse management problems stemming from the need to create a different box for each type of tile. Until now companies have hand to manage large quantities of cardboard that often ends up being unused and occupies enormous space in the warehouse, resulting in indirect management costs and large amounts of tied-up capital.
4Phases from System meets the need for the maximum flexibility and can rapidly cater for any supply requirement. The plant consists of sorting and packaging systems and is capable of forming the boxes directly in the machine. Starting out from a flat neutral cardboard sheet, it forms a box that is tailored to the product and takes account of all variations in calibre and stack height. The savings in terms of cardboard can be as much as 50% in the 60x60 cm size. This system offers enormous advantages due to the fact that it uses neutral cardboard, which allows the ceramic company to make boxes in-house without the need to commission an external box supplier. The need for double blanks for natural and rectified materials is eliminated and the problems of warehouse stock and obsolescence are solved, making for considerable space savings. In particular for producers with different brands and different sizes, the process solves all packaging supply problems. Furthermore, the graphic design of the blanks can be customised on the machine, allowing for an extremely short time to market. 4Phases also allows for savings in terms of personnel. It can continue to operate independently for between 8 and 12 hours and less work is required from the purchasing department for reordering blanks. Last but not least, it reduces the fire risk coefficient, thereby improving safety and cutting insurance costs.
The new automatic vertical warehouse from System Logistics has been redesigned in terms of its main components and provides a greater useful storage area but a smaller footprint. The considerable speed of movement of the trays (100/hour) places Modula Lift at the top of the market in terms of characteristics and performance.
Modula Lift is a big step up from the previous model and is ideal for storing and retrieving objects, components and semi-finished and finished products in any product sector due to its high storage capacity (60,000 kg net and more than 840 sq.m).
The elegant and modern design consists of an internal structure made from loadbearing profiles and modular steel casing entirely produced by a hi-tech production line. The structure holds the metal trays which are picked up and deposited in picking bays by means of an automatic elevator managed completely by an innovative and easy-to-manage integrated hardware and software system to make the storage operations rapid and efficient.
Together with its outstanding new performance characteristics, Modula Lift also guarantees greater respect for the environment and energy saving. The lower energy consumption is achieved by the use of lower power and more efficient motors than on the previous model. The 3 kW vertical axis motor, also used on the 750 kg model, allows for a considerable energy saving, while the optional Modula Green device delivers further savings by recovering the energy produced by the downward movement of the trays which would otherwise be lost. Thanks to this optional device, the payback time can be calculated at just a few months.
The modular and flexible Modula warehouses are ideal for any industrial sector and, with numerous models of various sizes, can be adapted to the various spatial needs of industrial facilities.
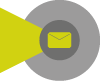
Did you find this article useful?
Join the CWW community to receive the most important news from the global ceramic industry every two weeks