Tecnargilla Preview _ System: the new generation Rotodigit
At Tecnargilla, System is introducing major innovations for digital decoration with a new generation Rotodigit; the revolutionary 4Phases machine for packaging ceramic tiles; the enormous range of low-thickness products manufactured with Lamina technology; and the new Freesize laser cutting machine.
Rotodigit is a digital printing system that can be applied to Rotocolor decoration lines. Rotodigit can be used to decorate any ceramic surface – even textures and edges – with excellent results in terms of reproducing natural stone, marble and granite and in decorating over relief and textured surfaces or in a double pressing process. The key characteristics are: the possibility of performing printing synchronised with Rotocolor rollers and having independent print units for each ink; an ink recirculation and print head protection system; the availability of three different decoration technologies; and the possibility of incorporating various technologies within the same overall dimensions so as to optimise space management.
4Phases constructs the boxes directly in the machine, starting out from a flat neutral cardboard sheet and forming a box that adapts to the product and takes account of all variations in calibre and stack height. Following a system consisting of quality control (Qualitron) and a new-generation distributor which automatically picks up the pieces divided into homogeneous classes and transfers them to a static platform, it performs the packaging process directly in the machine. By creating a continuous strip of cardboard within the machine, 4Phases is capable of forming boxes for different product sizes with an extremely rapid size changeover. It can also customise cardboard printing within the machine, which is performed before the box is closed. The Freesize system revolutionises the ceramic sheet cutting process, increasing productivity and reducing waste compared to the traditional process. Due to the absence of water, the Laminam® product is cleaner to handle and does not require drying, which brings considerable benefits in terms of environmental impact.
Dry cutting is performed in three steps:
- Grinding to remove the fibreglass at the cutting points, at a maximum speed of 60 m/min. on an automatic numerically controlled portal table with fixed platform and belts for automatic transfer. The grinding benches designed by Lamina assure ergonomics and worker safety by means of an integral closure system with X protections. Noise and dust are also minimised. Precision is guaranteed in the positioning movement and during the removal operation by latest generation systems. Next, an automatic overturner rotates the sheets by 180° so that the side without fibreglass layer is positioned on the cutting table for incision on the upper surface.
- Incision of the surface is performed on a computerised numerically-controlled portal table with maximum stability and minimum oscillations. The incision is made using a new specially designed laser system with excellent efficiency and durability capable of maintaining a constant speed of 60 m/min. on even the most delicate surfaces and reaching peak speeds of up to 110 m/min. The laser system eliminates all contact with the surface, avoiding damage and the risk of micro-chipping, a particularly serious problem in the case of products with complex designs or textured surfaces.
- Shearing of the sheet along the grinding/incision lines to create the required sizes. Head, end and side offcuts are sent for disposal via crushing belts. The sheet is aligned and moved by means of a wheel system towards the dynamic shearing machine that separates the pieces along the incision by means of the pressure of the separating rollers. At the exit, the pieces are separated by a variable-speed motor-driven roller conveyor. After being positioned and centred, the sheets are transferred to the piece loading machine belt.
- All operations are controlled by a highly efficient latest-generation electronic system from Beckhoff.
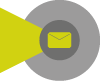
Did you find this article useful?
Join the CWW community to receive the most important news from the global ceramic industry every two weeks