The value of textured surfaces amid technological innovation and sustainability
Colorobbia’s Forma Plus family, with its GraffitiInks, NeoGrits and ExtraGlazes series, is designed specifically to achieve three-dimensional effects and surfaces and has been optimised with a strong focus on sustainability.
In recent years, the digitalisation of ceramic decoration has expanded the scope and number of digital applications. Following the airless application of engobes and glazes, today’s production lines now incorporate a larger number of printers, equipped with an increasing number of bars to expand the colour gamut and introduce digital effects and special effect inks. Additionally, two new processing areas – or blocks – have been introduced, one positioned before decoration and the other immediately after.
These two blocks allow for the creation of micro-reliefs, microstructures or even 3D structures using selective digital glaze, all starting from initially flat surfaces.
This hybrid full digital approach integrates multiple application technologies within the first and third blocks. In the first block, positioned immediately after the dryer, digital applications include glazes (full-field or selective 3D), water-repellent inks, and glue and grit. The third block, located after colour application, is dedicated to the digital application of solid materials, along with an additional application of glue and grit.
Forma Plus products
In 2023, Colorobbia introduced the Forma Plus family designed specifically to shape materials and achieve three-dimensional effects and surfaces. This product line offers a full range of applications through its subfamilies of inks and glazes in the GraffitiInks, NeoGrits and ExtraGlazes series. These applications can be performed both on the ceramic body as it exits the dryer (in the first block) and after the colour application phase.
One interesting emerging trend is the tendency to combine multiple functional effects, thereby enhancing both the three-dimensionality and the aesthetic quality of a tile’s finished surface. Several examples of this approach were showcased at Cersaie 2024. Instead of simply applying a three-dimensional or microstructure effect before or after the colour printer, these effects are now being combined in both the first and third blocks, either in synchronisation or with a completely randomised approach.
One interesting application involves combining a water-repellent GraffitiInk (applied at 50 g/m²) with a selective water-based digital glaze (applied at 400-900 g/m²). This combination results in a high-relief structure with an exceptional level of definition.
Sustainability
Remaining true to its commitment to protecting health and the environment, Colorobbia has optimised the formulation of the Forma Plus product family with a strong focus on sustainability. In addition to enhancing the technological value of the final product and ensuring compatibility with new application technologies, Forma Plus products also significantly reduce emissions of volatile organic compounds (VOCs, TOCs, aldehydes and formaldehydes) and odorous substances.
As part of these efforts, Colorobbia has developed two series of inks under the AIR family: AIR Evolution, a line of special solvent-based inks designed for high production performance, and AIR Evolution Aqua, a range of water-based inks designed to drastically reduce emissions, with emission levels directly proportional to water content. However, application of these inks at an industrial level can be more complex due to factors such as water percentage, which can pose a significant challenge if the digital printer operates on tiles that are still very hot.
While water-based inks are in some cases the only feasible option for reducing emissions, it is certainly possible to strike a balance between the need for greater sustainability and production performance, for example by carefully choosing where to position digital applications of water-based products along the production line. One particularly promising but underexplored application area is between the press and the dryer, where tile temperatures are around 25°C – significantly lower than the 90°C typically found at the dryer exit.
In terms of formulation, AIR Evolution solvent-based inks differ from AIR Evolution Aqua water-based inks in two key ways: the solid content is typically 10-30% in water-based inks and 30-50% in solvent-based inks; and the additives are non-polar in solvent-based inks and polar in water-based inks. The water content of AIR Evolution Aqua inks can vary between 15% and 40%.
Performance in terms of emissions
To determine the variations in emissions between different products from the AIR family, Colorobbia sampled the industrial emissions present in flue gases from a kiln when firing the same product printed with three different families of inks: traditional solvent-based inks, AIR Evolution solvent-based inks and AIR Evolution Aqua water-based inks. The findings revealed that AIR Evolution and AIR Evolution Aqua achieve fairly similar reductions in odorous emissions of between 45% and 60%, but their performance in terms of other types of emissions varies considerably. Water-based inks achieve significantly higher reductions in VOCs (70% or more), while AIR Evolution solvent-based inks show a better performance in reducing aldehyde and formaldehyde emissions.
A similar comparison was conducted for glues, evaluating the emissions generated by a solvent-based AIR Evolution glue compared with an AIR Evolution Aqua water-based glue. The results confirmed that, for products requiring a digital ink discharge of over 100 g/m² (colours + glue) and consequently a high glue discharge, a water-based glue is the only viable solution. A glue with a water content of approximately 40% was found to reduce odorous emissions by 70% and VOC emissions by 75%.
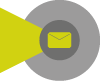
Did you find this article useful?
Join the CWW community to receive the most important news from the global ceramic industry every two weeks