Breton presents its new brand
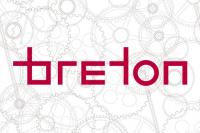
The new identity aims to reflect the new Group’s vision, which is focused to create bespoke services to improve the business performances of smart factories.
A new brand and a new vision for Breton (Castello di Godego, Treviso, Italy), world leader in the design and manufacture of state-of-the-art industrial machinery for processing natural stone, ceramics, metals and the development of engineered stone plants since 1963.
The company, counting a 280-million-Euro annual turnover (+35% over the last three years) and about 1,000 employees (more than 300 hired in the last triennium), will gradually replace its historic logotype throughout the 2020 with a brand new one, expressing Breton's high technological and pioneering essence.
“We decided to renew Breton’s identity system with the aim of enhancing the Group that is increasingly synonymous with global leadership, research and innovation”, announced Arianna Toncelli, Corporate Strategy Director. The new brand vision, stemming from an articulated “business identity” strategy, has been conceived to reflect the Group’s goal: offering its customers innovative and value-added solutions, products and services, capable of meeting even the unexpressed needs of a global market.
By moving from product to a “Product-as-a-Service (PaaS)” model, Breton widens its offer and keeps anticipating the companies’ needs.
In Breton Digital Hub a team of engineers, mathematicians and data-scientists is constantly at work to design, develop and improve software solutions that provide support to customers, by proposing new services - not necessarily related to Breton machines - that ensure full technological control over the processing plants. “Our mission - explains Federico Milan, Intelligence Manager - is to design modular software platforms that can be easily combined with and adapt to our customers’ needs, allowing them to increase both the productivity and the work quality of their companies”.
“In this way - adds President Luca Toncelli - we support the companies’ restart, by answering to their specific and increasing needs. The revolution started with Industry 4.0 led to the creation of new positions inside the company, like that of the Operation Manager. In a more and more data-driven paradigm, this increasingly required figure works with a mix of innovative and technological instruments (such as IoT, Big Data or Analytics) and uses data analysis software to orient the company’s choices and optimize its processes”.
Among Breton’s various solutions, there are computer systems developed to monitor the productivity of processing plants, provide predictive data on their life span, plan processes and identify problem-cause correlations, also using innovative concepts such as machine-learning. This proposal is completed by a wide range of services, such as the online purchase of spare parts, an easy access to all machine-related documentation, or software solutions allowing a vast number of operations, from kitchen design to costing.
Breton’s strategic business plan now aims at introducing innovation in the field of natural stone processing through Artificial Intelligence, thanks to the R&D project “Artificial Intelligence for Stone” which is supported by the Ministry of Economic Development.
Some “Digi Hub” software
Breton software proposal is articulated and constantly developing. From Sentinel, to monitor the performance and give real-time predictive data on CNC machines, to SkyNet, which collects data from the various machines of the processing line, providing information on the process and automatically adjusting its parameters.
The Smart Business Intelligence system makes a real-time analysis of the status and data of the whole plant through a customizable dashboard, which correlates information using analytics; this allows finding cause-and-effect relations quickly and solving possible process/product anomalies.
Smart Doc service, on the other hand, makes available all the machine, line or plant manuals, keeping the documentation always updated.
Thanks to Spare Parts, instead, Breton’s customers can also purchase spare parts or consumables directly online. Eventually, XPressTop Platform, a MES (Manufacturing Execution System) software, will allow performing several operations, from kitchen design to costing.
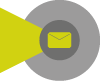
Did you find this article useful?
Join the CWW community to receive the most important news from the global ceramic industry every two weeks