Cotto Cusimano improves the efficiency of its firing process
The intervention, carried out by Marcheluzzo, significantly reduced the quantity of energy used by the kiln, while at the same time increasing the amount of thermal energy available to the dryer.
Refurbishing obsolete and consequently uneconomical plants is a complex operation, but if done properly it can bring enormous benefits in terms of productivity, safety and energy savings. Detailed knowledge of the production cycle together with a meticulous study of the existing lines is essential for the success of the operation.
Drawing on its extensive experience in the heavy clay sector and its expertise in supplying newly built plants, Marcheluzzo is able to extend the life cycle of machines already in service by incorporating state-of-the-art technology. One of the latest examples of a best practice concerns the revamping of the firing system at Cotto Cusimano.
A twofold challenge: higher performance with less energy
In 2022, Marcheluzzo completed a major revamping project at the factory owned by Cotto Cusimano, a dynamic, well-established company based in Settiggiano (Catanzaro) that has been producing fired clay pavers, facing bricks and roof tiles in a traditional and environmentally friendly manner since 1972.
The company, led by founder Andrea Cusimano with the support of his children and a team of highly motivated professionals, has embarked on a wide-ranging process of technological transformation based on an Industry 4.0 model, with special attention to reducing energy consumption and CO2 emissions. For this purpose, Marcheluzzo was commissioned to conduct a study aimed at improving the efficiency and cost-effectiveness of the firing process.
The first step involved upgrading the recirculating/preheating stage by installing four new independent high-pressure recirculating units designed to ensure an extremely uniform temperature across the entire width of the kiln. The firing curve was then improved by installing 4 new high-efficiency lateral burners in the initial firing phase and 2 new ceiling-mounted burners to maintain the temperature. The cooling phase was also completely overhauled. The installation of two combined rapid cooling units (intake and suction) complete with high-pressure fans equipped with inverters made it possible to manage the installed power according to requirements, while the new thermal room was designed in such a way that all the recovered air could be conveyed to the dryer. This was achieved using a system of automatic channels and baffles controlled by pressure transducers and thermocouples, which regulate the airflow according to the measured values while maintaining the kiln’s dynamic equilibrium. This improvement made it possible to rebalance the amount of air available to the dryer (kg/kal), an aspect that had not been optimised in the past, resulting in delays in the drying of material with a high residual moisture content.
The entire firing process is controlled by software, which displays the temperatures and a series of parameters to allow for remote process control.
Overall, the intervention carried out by Marcheluzzo significantly reduced the quantity of energy used by the kiln, while at the same time increasing the amount of thermal energy available to the dryer.
“The success of the operation is also down to the excellent teamwork between our technicians and the team at Cotto Cusimano,” said Paolo Marcheluzzo, CEO of Marcheluzzo S.p.A. “This continuous cooperation made it possible to complete the operation successfully and achieve better-than-expected results.”
Towards the digital and energy transition
The revamping of the firing process is part of a wide-ranging digital and energy transition project undertaken by Cotto Cusimano.
From an environmental perspective, the company is committed to implementing a business model that is attentive to the well-being of the planet and human beings. The installation of a 750 kWh photovoltaic array allows the company to self-produce 25% clean energy and, together with the plant improvements, to reduce its CO2 emissions by 12%. The company has also reduced its water wastage by 7% by recovering the water used for the fired material cutting, mould washing and wetting processes.
Processing waste is also recycled. Unfired clay scraps are mixed with the clay dried in the quarry during the summer; fired clay is recovered from the cutting and tumbling stages and fed back into production; and spent oil is reused for lubricating the dryer chains.
At the same time the company has innovated the technology required for the digital transition, such as the PLCs installed on the machines, the company management system and the MES software used to monitor productivity, all of which are systems that facilitate automated and interconnected production.
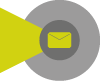
Did you find this article useful?
Join the CWW community to receive the most important news from the global ceramic industry every two weeks