VitrA inaugurated its “fifth plant”
With the new plant, equipped with Sacmi technologies, the Turkish company’s yearly sanitaryware production has surged to 6.7 million units.
On 18 October 2023, VitrA, Eczacıbaşı Building Products’ flagship brand and Turkish foremost exporter of ceramic sanitary ware, accounting for half of the country's exports in this sector for decades, celebrated the inauguration of its 5th facility in the VitrA Production Campus in Bilecik, Bozüyük. The new plant comes into operation just four years after introducing the second phase of VitA’s 4th ceramic sanitaryware plant in 2019.
Building on a 65-year history in ceramic production, this inauguration reflects a consistent approach of reinvesting profits to fuel growth and underlines VitrA's dedication to the intersection of innovation and sustainability.
Speaking at the ceremony, Bülent Eczacıbaşı, Eczacıbaşı Holding Chairman, stated, “With an investment of EUR 76.5 million, our newest facilities leverage advanced AI technology, ensuring end-to-end automation. Sustainability is ingrained in our business model. Our recent inclusion of a solar power plant at the VitrA Production Complex and the switch to I-REC certified green electricity exemplifies our dedication to zero carbon emissions.”
With this latest investment Eczacıbaşı Building Products is poised for remarkable growth. This strategic initiative not only aims to meet the surging demand and broaden market reach, but also to enhance operational efficiency and prioritize renewable energy.
Concurrently, VitrA's annual ceramic sanitaryware production has surged to 6.7 million units, with concealed cistern production reaching 2 million units. This expansion has led to a 50% increase in the Bozüyük campus's size, now spanning 469 thousand sq.m, and housing a workforce of 3,664 professionals.
Özgen Özkan, the CEO of Eczacıbaşı Building Products, remarked, “Our unyielding focus on marrying technology with human talent while safeguarding our planet's future has set the foundation for our continued growth. As we stand ready for Europe's burgeoning demand, our current 6.7-million-unit output positions us as in the top European manufacturers”.
Speaking about ongoing projects, Özkan also mentioned the decision to shift the concealed cistern production to the new facility:
“Our yearly production now stands at 2 million units. Additionally, with ongoing improvements in our faucets factory, we foresee a 50% increase in our faucet production by the end of 2024”, he said.
VitrA’s Fifth Plant is equipped with Sacmi’s most advanced technologies
VitrA was the first company to start the manufacture of ceramic sanitaryware in Turkey in 1958 and today it is a leading international Group producing and selling ceramic sanitaryware, with exports to 75 countries. The company is a long-standing close partner of Sacmi, which recently supplied all the key technologies for the brand new fifth plant set up at the company’s main base in Bilecik - Bozüyük.
«VitrA brought a brand-new concept to the culture of bathroom. Using the combination of comfort and technology, it transformed bathrooms into living spaces …….by giving priority to R&D and working with leading international designers»: this is how the company presents itself to the market and is the idea which lies behind the continuous growth and expansion of the VitrA brand on overseas markets since 1983.
RobotCasting
VitrA has chosen to dedicate its 5th plant to the production of the most elegant, complex and large-sized pieces - even up to 30 kg or more - in its range of products. To achieve this, it has purchased from Sacmi 5 new AVM cells, for a total of 10 casting machines and 2 AVB cells.
The high-performance reliable and flexible AVM machine is renowned throughout the sanitaryware world for its ability to produce complex pieces thanks to a modular platform which puts the mould at the centre of operations and allows the customer maximum freedom to manage automation systems and auxiliary equipment. Each cell is made up of 2 machines served by a robot which handles glue application, demoulding, piece transfer to the pre-dryer and handling up to automatic loading onto the car.
The FPV pre-dryer assists the piece ageing process, cutting time, saving energy and optimizing logistics. Also up and running at VitrA are the 2 new AVB 150, the multi-mould solution which will be dedicated to the casting of open rim WCs with a five-part mould and equipped with demoulding robot for an average production of more than 730 pieces per day. Manual operations are reduced to a minimum and are limited to piece inspection and loading onto the car at the end of the piece transport and deposit system, controlled by the robot, which assists in the piece ageing process.
Dryers
Once the casting and ageing stages have been completed, the pieces enter the new, intermittent driers supplied by Sacmi, two with 3 chambers (36 cars) and one with 2 chambers (12 cars). The outstanding feature of these machines is the optimized distribution of hot air, made possible thanks to the cone fans which guarantee maximum uniformity of air distribution with significant advantages in terms of process repeatability and constancy.
Each chamber is provided with a thermal output equal to 490 kW, adequate to carry out two drying cycles per day lasting 11 hours each. The result is a production capacity equal to, respectively, 1440 pieces per day (in the two 3-chamber driers) and 960 pieces (in the 2-chamber drier). The drying cycle takes place at a controlled temperature (90°C) to bring the residual humidity of the piece below 1%.
The punctual control of the drying curves is achieved by means of temperature and humidity probes and by the system which governs the controlled emission of residual air to guarantee optimum humidity and temperature parameters inside the chamber at all times.
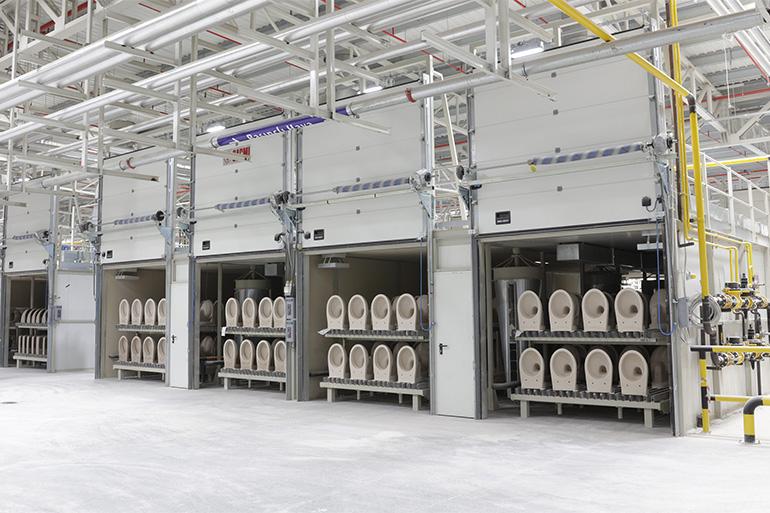
RobotGlaze
For robotized glazing of the pieces a total of 7 Sacmi RobotGlaze solutions have been supplied to VitrA for its new plant. This system was designed by VitrA and the Sacmi team together. Total automation of operations is the distinguishing feature of the solution specially configured with two handling robots for each cell which control movement operations and, in the case of WCs, transfer of the piece to the syphon glazing machines.
Each cell can handle from 730 to more than 1050 pieces per day, according to the production mix. During this stage, 4 new complete lines will be assigned by Vitra to the glazing of WCs and 3 will be dedicated to washbasins. The solution is provided with all the latest technology to optimize glaze consumption and recover overspray, from the exclusive Sacmi Mass Control® system to the solution for glaze recovery by means of water curtain filters.
A crucial part of the glazing cell is the Sacmi-Gaiotto GA-OL 9-axis (6 + 3 optional) robot, equipped with software for offline programming of the glazing recipes, already chosen by the customer. Glaze application is carried out by the GDA 80 spray-gun, Sacmi’s popular zero-maintenance solution which has had great success on the market.
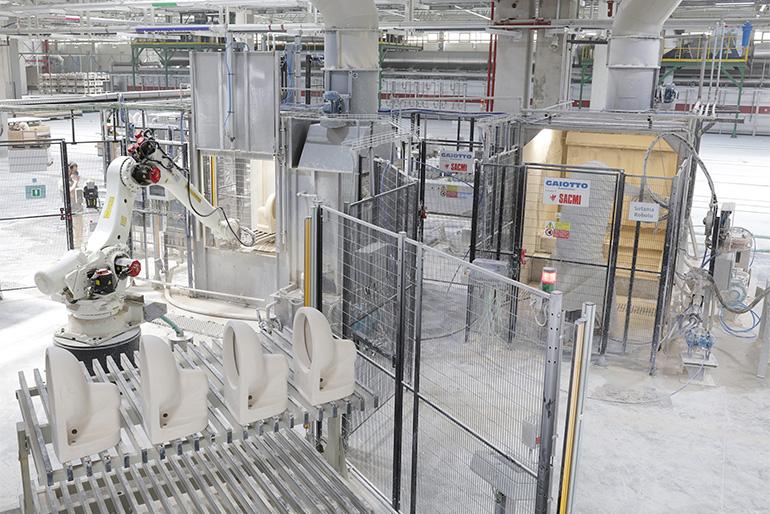
Kilns
To complete the Fifth Plant project, VitrA chose a state-of-the-art TWS Sacmi-Riedhammer tunnel kiln which is 135 metres long, 3.6 m wide, with a working height of 800 mm. Already up and running, the tunnel kiln can handle up to 135 cars holding 82 tons of product per day, equal to 3280 pieces of various types.
The kiln is equipped with EMS 400, Riedhammer’s top-of-the-range solution to recover air for pre-heating the combustion air to a temperature of 400°C. The result is a reduction in consumption, when operating at full capacity, equal to just 810 kcal/kg of product net and an optimum temperature distribution uniformity.
In addition to the tunnel kiln, Sacmi also supplied a shuttle kiln – the 18 m Pulse Firing HWS – equipped with 12+12 cars to handle a total of 720 pieces/cycle with the standard mix of pieces (equal to approx. 20 tons of product). In this case too, maximum attention was given to the reduction of energy consumption equal to 1380 kcal/kg of product net at full capacity during second firing.
One of the special features of the Sacmi-Riedhammer HWS is the “double door” configuration to facilitate loading and unloading operations thus increasing the amount of time the kiln is available for firing. The solution is also equipped with all the latest technology for automation of handling operations from placing the pieces in and out of the cars to control of the movement system.
Finally, in order to respond to VitrA’s need to meet stringent emission limitation requirements, the combustion system of both kilns – tunnel and shuttle - is already set up for the use of hydrogen. In this way VitrA seals its reputation as a forward-looking environmentally aware company which can rely on SACMI as an ideal partner.
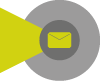
Did you find this article useful?
Join the CWW community to receive the most important news from the global ceramic industry every two weeks